www.industry-asia-pacific.com
07
'15
Written on Modified on
100% clean cut – fineblanking sets its own standards
Cost-efficiency and precision in the series production of complex components – fineblanking scores with a whole range of user benefits. The process opens up new technical approaches to manufacturing large numbers of ready-to-install multi-functional parts and offers new ways of maximizing cost efficiency. Its versatility with regard to parts geometry and complexity and scope for reducing the number of downstream operations makes the technology extremely interesting from several aspects.
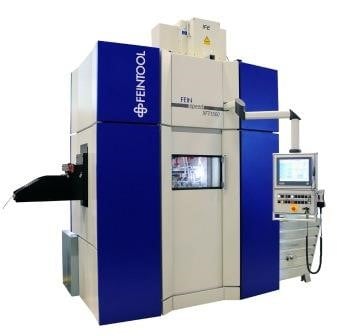
The precise interaction of three forces has a crucial influence on the quality and performance of fineblanking. At the start of the process, the active forces are the vee-ring force and counterforce. The vee-ring force presses a toothed vee-ring into the material and the counterforce presses the sheet metal strip against the punch. Even before the blanking process begins, the material is firmly clamped from both sides of the enclosed shear periphery. Only then is the third force, the blanking force, applied, cutting the part while it is clamped.
Today, Feintool is the leader in fineblanking technology and the sole global supplier of the entire fineblanking process, from fineblanking presses and peripherals through to tools – entire systems from a single source. Parts design, prototyping, engineering and tool design represent another focus area.
Greater complexity level of cut geometry
The formability of the materials from which parts are made, their thickness and the maximum load which the tool's cutting elements can withstand are generally responsible for limiting the potential geometry of the cut. However, ongoing developments in the field of tool materials coupled with intelligent ideas for designing blanking processes are helping to significantly expand fineblanking's scope. Car seat adjuster parts with precision engagement teeth are one current example. Tooth size equates approximately to a module size of between 0.3 and 0.5 for material thicknesses of between 3 and 6 mm.
Exponential increases in output
Huge progress has also been made on potential outputs. Improvements have addressed not only the maximum stroke rate per unit of time, but also the length of time the entire production system is capable of running without interruption. Feintool has achieved advances primarily by developing appropriate servo presses. The manufacture of car door lock components provides an example. In a single stroke employing an overall force of 450 tonnes, four plunger blocks can be cut simultaneously from the material strip at an average cycle rate of 100 strokes per minute.
Increased component complexity
Complex 3D parts represent a further focus of development activities. Manufacturing them requires an increase in the usable space available on press beds. A different approach is to exploit existing geometries and forces more efficiently. One area involves multifunctional tool stages that use the multi-acting machine forces to produce a succession of processes in one and the same step.
Integration of downstream operations
A similar pattern emerges when it comes to integrating downstream operations into the main process. A typical example is combining fineblanking (including burring) with subsequent deburring of the flat parts, followed by a bending process. Integrating several processing stages into a single tool makes parts production faster and more economical. In addition, this considerably extends the service life of tools between regrinds.
Reduced material usage
Material is valuable and often accounts for more than 50% of unit cost per part. Consequently, the width of the scrap bridge outside the fineblanked contours and the space required for auxiliary functions in the skeleton strip need to be reduced as much as possible. The key to success can be found right at the start of the planning phase. The best results, i.e. savings in material and therefore costs, can only be achieved by early consideration of the interaction between the component design, material and tool design.