www.industry-asia-pacific.com
11
'22
Written on Modified on
ACHIEVING STAGE V COMPLIANCE WITH RENTAL GENERATORS
Studies validate this approach showing that diesel exhaust emissions contribute significantly to air pollution, accounting for 15% of the nitrogen oxide (NOx) and 5% of Particulate Matter (PM) emissions in the EU. In particular, they show that the particle size in diesel soot impacts observed health effects.
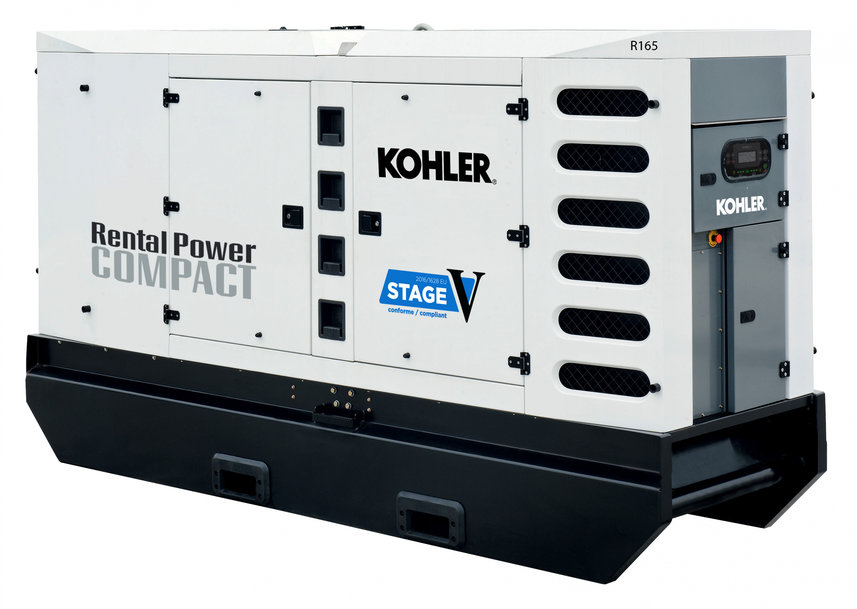
Stage I emission standards were first introduced in 1997. Since then, each stage has progressively made the emission limits more stringent, with Stage V coming into force in 2019 and 2020. The phased introduction of Stage V allows for existing non-compliant generators to remain in use. However, local authorities and municipalities are creating low emission zones, which enforce the use of Stage V generators. The regulations focus on particulates and NOx emissions for non-road mobile machinery (NRMM), especially mobile generating sets.
Several factors have contributed to the ability of diesel engines to meet each new stage of the regulations. Fuel quality improvements, engine efficiency, and exhaust gas treatment have all played a role. For Stage V compliance, Diesel Particulate Filters (DPFs) are critical for controlling exhaust gas particulate emissions from larger gensets.
Kohler has a long history of support to the energy industry and a track record of developing diesel generators that meet the latest environmental regulations.
Stage V in greater detail
Stage V regulations apply to a wider range of NRMM by including both smaller and larger capacity engines than previously covered. Particulate emissions have been the focus of attention since Stage III B, which introduced a PM limit for the first time. In practice, many engines were able to meet these requirements using in-cylinder technology. However, this approach will not be sufficient for Stage V limits in larger gensets.
Stage V demands an improvement in particulate control by introducing a particulate number (PN) limit, which relates to particle size. There is also a reduction in the PM limits compared to Stage IV. These specifications effectively enforce the use of wall-flow particulate filters. Additionally, Stage V regulations are more stringent on NOx emissions. The new NOx limits require additional exhaust gas treatment for larger gensets.
Stage V regulations define emission limits based on engine power. The new regulations were introduced gradually, with engines below 56 kW and above 130 kW covered from 2019. In 2020, this cover was extended to engines between 56kW and 130 kW. Stage V also applies to compression ignition (CI) engines below 19 kW and above 560 kW and spark-ignited (SI) engines above 19 kW. Other previously unregulated engines like Category NRG generator set engines above 560 kW are also included. The following table summarizes the Stage V emission limits.
Stage V rental solutions
The trend towards increasing emission requirements is likely to continue, putting pressure on the rental generator sector to comply. This has already led to several advances in engine technology. Emissions targets are more achievable with smaller engines due to the lower fuel consumption, but larger engines require several emission reduction elements.
The starting point for emission control is minimizing fuel usage. Common Rail injection systems are key to this approach. Their optimized computer calibration ensures that engines run at maximum efficiency. On smaller engines, this element alone may be sufficient for the machine to meet Stage V requirements.
Exhaust gas recirculation (EGR) is the next step in emission control. An EGR valve manages the quantity of exhaust gas by cooling a portion of these gases and re-injecting it into the engine intake. Burning these exhaust gases limits NOx production.
Post-treatment systems limit exhaust emissions further. A diesel oxidation catalyst (DOC) transforms carbon monoxide gases, hydrocarbons and nitrogen oxides into water, carbon dioxide and nitrogen dioxide. The reaction takes place as the exhaust gases pass over a honeycomb structure covered with catalyst metals.
The final step in emission control uses a diesel particle filter (DPF). The filter collects particles and burns them using heat from the engine and DOC. When a DPF has accumulated a large mass of particles, it must be regenerated, which can be accomplished in a few different ways:
- Passive regeneration occurs when exhaust temperatures are high enough to burn any remaining particles. These conditions are only met when the charge is high.
- Active regeneration requires injection of a fine fuel mist into the exhaust line to increase the exhaust gas temperature and burn the soot (particles). Both passive and active regeneration can be automatically initiated by the engine controller.
- Stationary regeneration happens during a maintenance outage. This is required when operating conditions make both passive and active regeneration impossible. Due to the interruption to operations and the need for manual intervention, it is desirable to limit the frequency of stationary regenerations. One way to achieve this is to use a ballast resistance device that automatically increases the minimum load on the machine. This load control will space out the DPF regenerations, thus limiting the need for operator action and generator downtime.
Engines above 58 kW can also benefit from selective catalytic reduction (SCR) to reduce NOx. A urea-based additive called diesel exhaust fluid (DEF) contains ammonia which mixes with exhaust gases in the presence of a catalyst. SCR converts NOx into nitrogen, carbon dioxide and water vapor.
The stringent requirements of Stage V regulations make it imperative for operators to have a continuous view of the engine performance and compliance. Kohler's APM403 controller with its user interface allows for fingertip access to all the relevant information. It displays parameters like soot and ash rates in the particle filter and which type of regeneration is in progress. The controller also manages the load distribution of the ballast to space out manual regeneration intervals as far as possible.
Kohler has introduced a wide range of rental generators to meet the Stage V requirements. The range covers the 20 to 550 kVA power ratings with the KOHLER engines for the lower power demand generator sets from 20 to 50 kVA. John Deere engines drive the 110 kVA to 550kVA models. The R20C5 is a 20 kVA generator set, which achieves Stage V compliance using diesel injection controls. However, the R330C5, a 300 kVA machine, uses an entire pollution reduction technology package, including selective catalytic reduction with urea injection.
Conclusion
Stage V is the latest revision of regulations targeting the emissions of non-road mobile machinery (NRMM), focusing on particulates and NOx emissions. A new standard for particulates called particulate number was introduced in Stage V, which is driving the use of particulate filters as an exhaust gas treatment technology.
Some smaller generator sets can meet the Stage V limits by controlling diesel injection to the cylinders, but larger models require a more comprehensive solution. This solution could include exhaust gas recirculation, diesel particulate filters, diesel oxidation catalyst and regeneration, as well as selective catalytic reduction with urea injection.
Kohler has 100 years of experience in the power industry as an industrial generator manufacturer. They maintain an extensive knowledge base and the technical capability to develop compliant and optimized products. Kohler’s commitment to the industry is demonstrated by keeping abreast of incoming regulations, including Stage V requirements and ongoing investment into research and development. As such, Kohler is a trusted partner for the rental generator set market.
www.kohler.com
The stringent requirements of Stage V regulations make it imperative for operators to have a continuous view of the engine performance and compliance. Kohler's APM403 controller with its user interface allows for fingertip access to all the relevant information. It displays parameters like soot and ash rates in the particle filter and which type of regeneration is in progress. The controller also manages the load distribution of the ballast to space out manual regeneration intervals as far as possible.
Kohler has introduced a wide range of rental generators to meet the Stage V requirements. The range covers the 20 to 550 kVA power ratings with the KOHLER engines for the lower power demand generator sets from 20 to 50 kVA. John Deere engines drive the 110 kVA to 550kVA models. The R20C5 is a 20 kVA generator set, which achieves Stage V compliance using diesel injection controls. However, the R330C5, a 300 kVA machine, uses an entire pollution reduction technology package, including selective catalytic reduction with urea injection.
Conclusion
Stage V is the latest revision of regulations targeting the emissions of non-road mobile machinery (NRMM), focusing on particulates and NOx emissions. A new standard for particulates called particulate number was introduced in Stage V, which is driving the use of particulate filters as an exhaust gas treatment technology.
Some smaller generator sets can meet the Stage V limits by controlling diesel injection to the cylinders, but larger models require a more comprehensive solution. This solution could include exhaust gas recirculation, diesel particulate filters, diesel oxidation catalyst and regeneration, as well as selective catalytic reduction with urea injection.
Kohler has 100 years of experience in the power industry as an industrial generator manufacturer. They maintain an extensive knowledge base and the technical capability to develop compliant and optimized products. Kohler’s commitment to the industry is demonstrated by keeping abreast of incoming regulations, including Stage V requirements and ongoing investment into research and development. As such, Kohler is a trusted partner for the rental generator set market.
www.kohler.com