www.industry-asia-pacific.com
21
'19
Written on Modified on
DMG MORI’s new turning machine includes igus® readychains
Pre-assembled cable carrier systems help create revolutionary piece of technology.
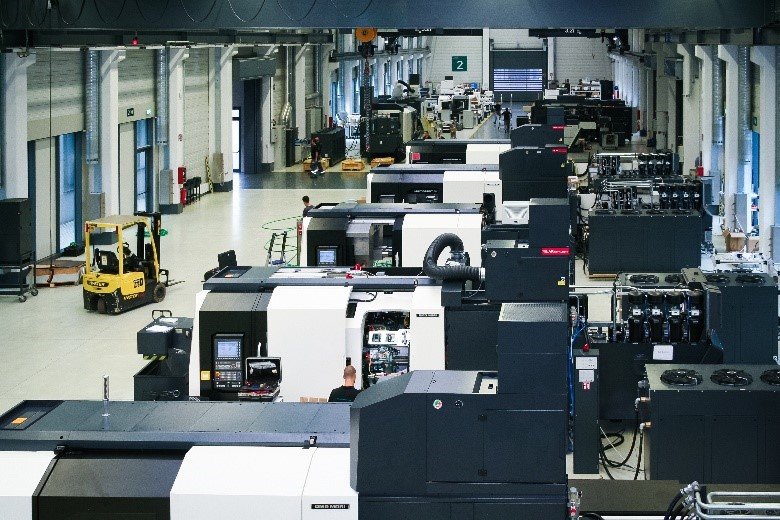
DMG MORI, an industry leader in the manufacturing of machine tools, has developed a new automatic turning machine with multiple spindles that represents a technological revolution in producing turned and milled parts in both boring and bar machining.
After only two years of development, the company designed MULTISPRINT, which are multi-spindle automatic lathes that offer unlimited possibilities with enhanced efficiency and fast, precise, and diverse production processes. Key components to the MULTISPRINT series are readychain harnessed energy supply systems from igus, the Germany-based manufacturer of motion plastics. The machine is the first to combine a multi-spindle automatic lathe with SWISSTYPE technology, and with a Y-axis on each spindle position.
The MULTISPRINT series combines the efficiency of a production turning machine with the precision of a turning machine and the complexity of a universal turning machine. The units make complicated turned and milled parts in the areas of bar machining without re-tooling the system.
“Customers are thrilled and immediately understand the concept of the new machine,” said Mikro Passerini, Technical Director at DMG MORI’s Italian location GILDEMEISTER Italian S.p.A. “They especially like the ease of maintenance that the igus energy supply system enables.”
Changing requirements for turning machines
Customer requirements for modern turning machines have changed due to market dynamics and globalization. Machine tool makers now demand shortened processing and tooling times, reduced effort for process development and integration, and an ability to handle the increasing degree of complexity.
The new MULTISPRINT includes, for example, nozzles for fluid power equipment, implants for dentistry and shafts for motor vehicle manufacturing, which are just three of the complex components that can be made on high-tech machines. The result is a manufacturing solution for scalable requirements from initial series production to the high-volume production of complex workpieces.
The combination of three types of machine technology enables the customer to engage in completely new forms of production, setting new standards in productivity and efficiency. The customer enjoys maximum flexibility for the mass production of components with a diameter of up to 50 millimeters.
Pre-assembled cable carrier system
The igus readychain, two meters wide and weighing 750 kilograms, powers the machine. Among the first challenges for engineers was ensuring that the energy chain system fit into the housing of the machine.
The system includes eight energy chains, 64 electric cables and 73 hoses. The construction has a 1.8 meter-high body for rotation. Six linear energy chains for driving the spindles protrude from the body like arms. Lifting the unit, which requires the assistance of two cranes, and connecting the readychain to the spindle drum requires about two hours.
During product development, technicians and engineers worked for nearly five months to design and assemble the machine, test it and send it on its travels. It was finally unveiled at EMO in Hannover, Germany, where it was presented as a revolution in mechanical engineering.
www.igus.com