www.industry-asia-pacific.com
14
'19
Written on Modified on
readychains accelerate productivity for machine and plant builders
Manufacturers can improve efficiency with harnessed energy chains.
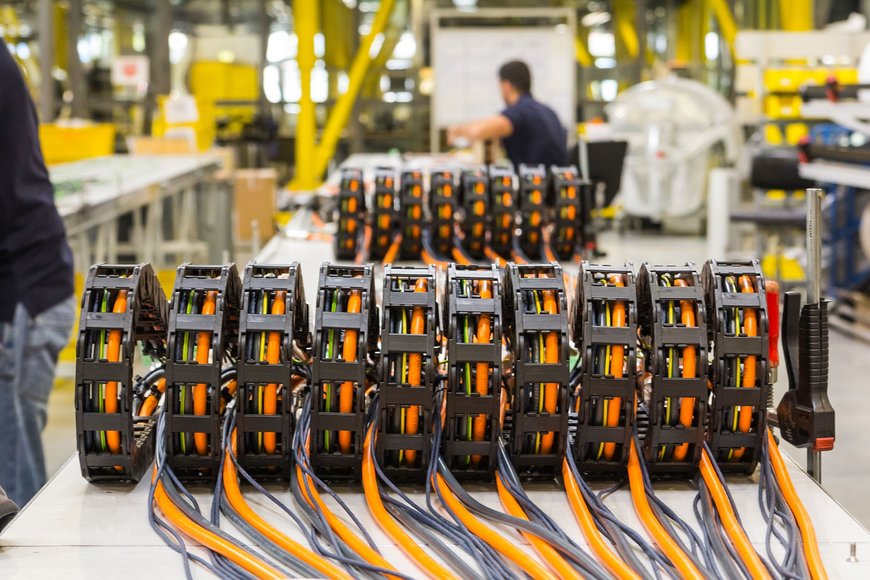
Readychain systems provide an economical and swift solution and are being used in thousands of applications around the globe. igus, which runs its North American operations out of Providence, R.I., has simplified the procurement process with one-stop shopping that makes readychains easy to purchase and install.
The company maintains the high-quality of the in-house produced readychain systems by constant innovation of the automation processes. Machine and plant builders now have the ability to recognize how readychain systems can accelerate and improve productivity.
Technical creativity and a quest for perfection
igus has built a wealth of experience in the industrial process over the years. New concepts for energy supply systems are constantly being developed which can be integrated in a production or production line with an almost precise fit.
The technical creativity and the desire to deliver perfection to the customer is another building block. For mechanical engineers, this is reflected in a broad range of chains and cables and an attractive price/performance level.
Factory work is not more expensive
igus has its own space where more than 90,000 individual components, more than 1,300 chain-compatible cable models and an estimated 3,500 electrical components are stored. The essential benefit, besides efficiency with no minimum order quantity, is the short delivery time.
Manual work at igus also means the immediate production start of a chain after the order is issued by the plant manufacturer. Delivery times in as few as 3 to 5 days ensure that the tailor-made chain can be installed promptly at the customer’s plant – significantly accelerating production.
Quick installation of the harnessed energy chain is not the only recognizable advantage for mechanical engineers: lean storage in their own company means more space in their own factories for the pre-assembly of new machines or for a factory acceptance test before delivery to the end customer.
The savings of harnessed readychains are also noticeable in the purchase: one chain, one procedure, one task, one order number – all this becomes a significant productivity accelerator, in addition to swift assembly.
Another key aspect of readychain’s success is that plant manufacturers do not have to build up or maintain any specific know-how about energy supply. After all, designing and implementing energy supply systems for dynamic applications is anything but trivial.
Often there are small structural hurdles or practical obstacles that make it difficult to bring together cable and energy supply at the interface. If the installation takes longer or there are errors during commissioning, this can immediately have a negative impact on the overall budget.
Intuitive handling makes everything easier
If you are planning to use readychains in your system, you can immediately install functional units made of cable and plug-in connectors, perfectly matched to the chain. Fast, because a “talking” label makes installation on the machine an intuitive action. This is where electricians and mechanics benefit tremendously, because someone without specialist knowledge can also make the connection.
That’s quite different from self-made energy supply systems, where dangers often lurk in the installation of connector-cable connections. The most important factor in plant construction today is time. And the installation of cables in energy chains can cost a lot. The harnessing is just a set screw with which igus solves these problems.
Modular racks: precise work at the interface
Customers are even more efficient in designing their processes when they install their energy chains on a machine using the readychain rack, the base frame for transport and assembly.
By means of traversing units, the modular rack moves the harnessed energy supply systems to the appropriate interface with millimeter precision and in an uncomplicated manner. At the same time, the individual concept stands for even greater cost awareness: the use of such a rack pays off with just a few machines – a strong argument for companies that produce small batches.
With the help of the readychain rack, a technician completes the installation of the harnessed energy chain within one day on average. The telescopic design makes the rack indispensable especially for those companies who want to stay flexible with the chain lengths. The transport and assembly rack can be adjusted to the new chain length with just a few simple steps.
The combination of harnessed chains and the readychain rack reduces process costs significantly and, above all, in a sustainable way. Also, the modular design of the transport rack allows adjustments to new conditions at any time. The reusability feature not only protects the project budget, but also helps the environment.
If, for capacity reasons, companies are unable to implement the installation of a harnessed chain on their system, igus offers an installation service. The use of trained and experienced assembly experts ensures timely and correct installation, and helps manufacturers comply with important deadlines even in times of bottlenecks and order peaks. All customers are offered a system guarantee, which the company offers to all customers and is confirmed by the quality standard DIN EN ISO 9001:2015.
The basis of this guarantee is the pursuit of new technical achievements and the constant optimization of tested and certified quality standards in the production of complete systems – with the goal of being the best service provider with the highest quality, both technically and in customer service. Countless specific and general product certificates, test and quality seals and approvals demonstrate igus’ priority to deliver quality readychains.
If the quality of a harnessed chain does not meet the customer’s demands, a service team is available for timely repair.
The combination of manual work and partial automation in chain production, superior customer service and fast response times are examples of the efficiency and productivity acceleration that igus offers its customers with the readychain concept. This is not only limited to Germany as readychain support centers are located around the world.
China, the United States, Taiwan, Brazil, India, Japan and South Korea as well as South Africa, Great Britain, Poland, Italy and Spain have support centers that guarantee a consistently high quality, quick availability and uniform parts list. This set-up optimizes assembly time as well as logistics and procurement processes for customers everywhere.
www.igus.com