www.industry-asia-pacific.com
24
'16
Written on Modified on
Cycle time reduced from 41 seconds to 27 seconds.
ProfitTurning™ - The cutting edge of tomorrow’s CAD/CAM software
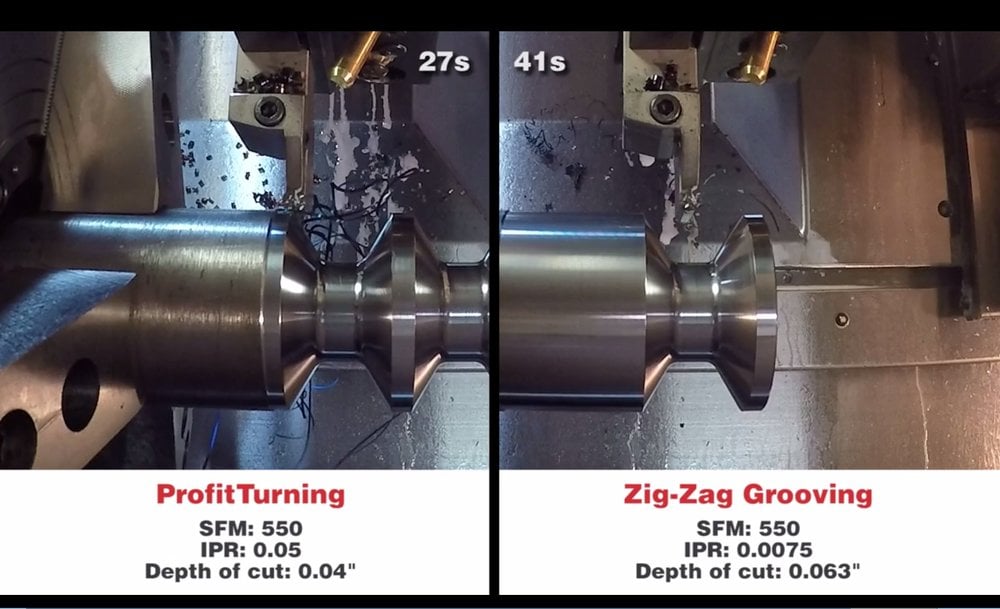
ProfitTurning™ is a high-speed lathe roughing strategy developed by DP Technology Corp. for OD/ID/face cutting and other tasks. Fast, secure and efficient, it also extends tool life by significantly minimizing wear. Compared to conventional ramping methods, ProfitTurning™ reduces machine cycle time as well as the frequency tooling inserts need to be replaced.
DP Technology’s R&D Director of Product and Engineering Ivan Kristic reveals the science behind ProfitTurning™’s performance:
“ESPRIT 2016’s ProfitTurning™ toolpath maintains consistent cutting forces and chip loads, allowing cutting speeds to be significantly increased. By employing trochoidal turning and controlled engagement techniques, the ProfitTurning™ toolpath also reduces vibration and residual stresses, which in turn makes it particularly well-suited to thin walls or hard materials, especially super alloys. The net result is significantly reduced cycle times and maximized productivity.”
Physics-Based Cutting Engine
ESPRIT 2016 uses a physics-based cutting engine which provides the foundation for the technologies such as ProfitTurning™.
While traditional cutting strategies consider only the geometry of materials, ESPRIT 2016 taps deeper into the science of how different industrial materials can be cut in the most efficient ways possible. Its new toolpath technology uses the principles of physics to formulate unique strategies for each cutting challenge.
To do that, ESPRIT 2016 inputs all relevant factors in the toolpath algorithm such as tool material, tool shape, workpiece material, tool speed, feed rate, chip deforming, chip load, machine tool power, acceleration and deceleration. This helps establish complete control of the cutting environment, allowing for optimal cutting everywhere along the toolpath.
For more details about this new technology, please read the ESPRIT 2016 ProfitTurning™ White Paper available at www.espritcam.com/products/profit-turning.