Siemens to add new simulation software for drives to Industrial Operations X offering
At this year's Hannover Messe, Siemens is presenting Sinamics DriveSim Advanced, an extended simulation software for drive constellations that can be used for both engineering and commissioning on the basis of a digital twin.
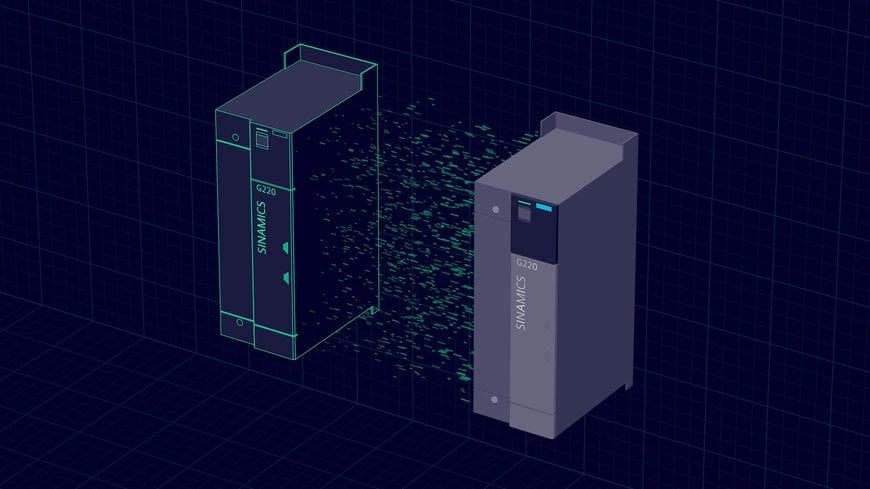
Siemens is presenting Sinamics DriveSim Advanced, an extended simulation software for drive constellations that can be used for both engineering and commissioning on the basis of a digital twin.
- Sinamics DriveSim Advanced expands the Industrial Operations X offering, part of the Siemens Xcelerator digital business plattform
- Sinamics DriveSim Advanced simulation software for virtual engineering and commissioning of drive constellations
- Complete digital twin of Sinamics drives with all parameters and configurations
- Extending digitalization of drive technology continuously enables machine builders to reduce resource consumption and optimize energy efficiency
Sinamics DriveSim Advanced thus expands the simulation portfolio for motion control drives at Siemens, which was introduced to the market in 2021 with Sinamics DriveSim Basic. At the same time, Sinamics DriveSim Advanced adds to the Industrial Operations X offering. With Industrial Operations X, Siemens offers a continuously growing interoperable portfolio of products and services for production engineering, execution, and optimization. This offering brings more information technology (IT) and software capabilities to automation and production operations, making industrial operations more adaptable. The Industrial Operations X portfolio is characterized by supporting an open ecosystem, being flexible with modular and scalable functions, and enabling interoperable, seamless, holistic production value chains.
In this context, Siemens offers Sinamics DriveSim Advanced, a comprehensive solution for the simulation of drives that offers a realistic simulation of the new Sinamics converters with all their functions. Users can create a digital twin of the drive in a virtual environment with all the parameters and configurations that correspond to a real drive. The innovative technology and user-friendly interface allow users to simulate, commission and optimize the behavior of drive systems in a virtual environment before building them in the real world. This significantly increases efficiency and productivity when optimizing drive systems and machines. With Startdrive, simulation is integrated directly into TIA Portal, so no additional software tools are required. Using the digital twin, the logical and functional aspects of the drive system can be simulated identically to the real Sinamics drives, while electrical, magnetic, and mechanical aspects are partially modeled in a simplified way. The use of virtual commissioning and engineering tools such as Sinamics DriveSim Advanced thus enables machine builders to reduce resource consumption and optimize energy efficiency, leading to a more sustainable approach to machine building.
Shaping the future of production sustainably with energy-efficient drives
With the continuous expansion of its digitalization portfolio in the area of drive technology, Siemens is responding to the current needs of industry for greater sustainability. Electric motors are responsible for over 70 percent of industrial energy demand. Simotics SD IE4 motors and IE5 motors are already very energy-efficient with an efficiency of up to over 96 percent and are therefore also optimally designed for operation directly on the grid. By using motors of the very high efficiency classes IE4 and IE5, savings of 6 percent of electrical energy on average are possible. Using perfectly matched motor and drive systems for variable-speed operation of pumps, fans and compressors, energy savings of 30 percent on average can be achieved, and in some cases even more. The real key to greater energy efficiency, however, lies in the overall system: In the interaction of all individual measures - from more efficient motors with variable-speed control, to digital system components and tools, to the use of electrically buffered energy in the motor network - savings of 60 percent on average can be achieved in the system network.
www.siemens.com