Versatile working machines thanks to electronic control of open-circuit pumps
Manufacturers of mobile machines must decide whether to control their pumps using pressure, torque or the swivel angle – and must compromise as a result. The same applies to numerous other parameters which are defined once for the hardware and continue throughout the machine’s service life.
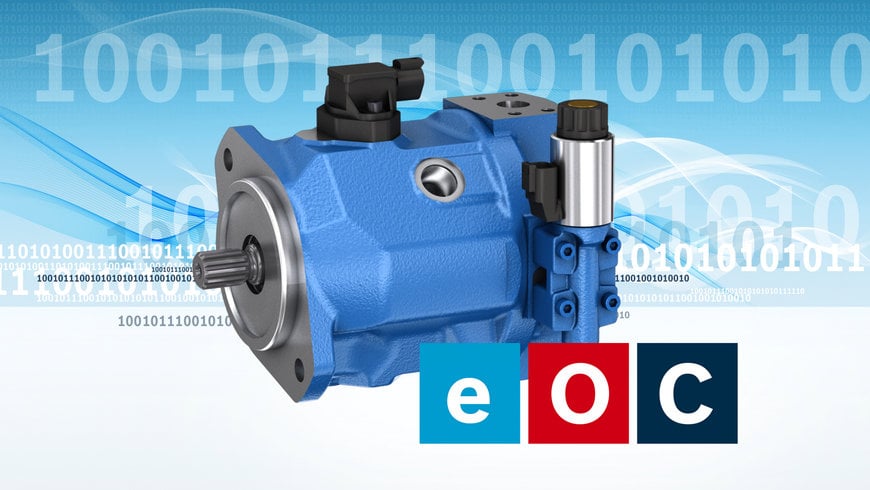
Electronically controlling hydraulic pumps in open circuits with Rexroth eOC opens up new possibilities in working hydraulics.
- Marketable hydraulic architecture for mobile machines
- Software and components optimize the potential of machines
- In the future, travel and working hydraulics systems can be in a single circuit
The new electrohydraulic solution from Bosch Rexroth solves this problem by moving control functions from the hydromechanical controller to the software. This makes machines even more versatile and flexible. In addition, machines benefit from increased productivity and lower energy consumption.
The eOC pump – the central component
The electrohydraulic eOC pump with swivel angle sensor and pressure sensors is the central component in the eOC architecture. It ensures the proper control of the necessary setpoint values for torque, pressure or flow. The pump provides highly dynamic control with millisecond accuracy to modulate the pressure. In combination with the eOC software, characteristics such as dynamics and power control can be set, changed and combined.
eOC software for machine optimization
Controlled via a CAN interface, the eOC software makes it possible to set various control parameters flexibly during operation. With hydromechanical control functions and interfaces moved to the software, control modes can be individually changed and combined during operation and the pump dynamics can be set variably. Pressure, torque, flow and the swivel angle are controlled independently of each other in an electronically closed control circuit.
With predefined parameters, the pump behaves optimally as part of the hydraulic system regardless of function. Via the CAN bus interface, setpoint values and parameters can also be adjusted dynamically to allow additional functions and to adapt machines to meet specific customer requirements and complete various work tasks.
The eOC software can be installed on a Rexroth BODAS controller or a controller from a third-party manufacturer. It constantly adapts the hydraulic power to the available engine torque and thus allows dynamic, precise work functions, which ultimately increase the overall productivity of the working machine. The energy consumption of the entire hydraulic system is optimized, resulting in lower fuel consumption or better battery use.
Marketable machine concept
Mass-produced machines already benefit from the new hydraulic architecture. They include a compact excavator which entered mass production in the first half of 2021. A power mode for demanding excavation work was developed for this purpose. This operating mode allows maximum pressure and torque as well as maximum pressure gradient dynamics, for example when emptying the shovel. The machine also has a fine mode allowing jerk-free, smooth operation, in applications such as laying pipes.
The eOC architecture is also ideal for use in wheeled excavators. In the past, numerous valves were needed to adjust the power in these multifunctional machines to suit the particular task. The switchover to the eOC architecture significantly reduces the hardware outlay, minimizes costs and avoids potential sources of error in valve switching.
Ongoing further development
As a scalable solution, the Rexroth eOC portfolio allows step-by-step implementation – from the electrohydraulic eOC pump with swivel angle sensor and pressure sensors to the option to cover the entire hydraulic system. An eOC main control block and an electric joystick are provided for this.
Bosch Rexroth has now upgraded a wide range of axial piston pumps and added numerous new functions to the existing basic concept. For example, the eOC architecture now allows the dynamic control of pressure, swivel angle and torque gradients. This means that the pump not only reaches a specific target value – the pressure gradients that are needed to achieve this pressure are also determined. This allows much smoother and gentler motion, especially at the start of a movement.
Auto-calibration, where the component is calibrated within the machine itself, is another new eOC function. Calibration therefore no longer takes place statically at the OEM’s end of production line – it is instead carried out cyclically while the machine is operating. The eOC software records specific calibration data every time the machine starts. Other data is recorded whenever the machine’s operating conditions allows.
In this case, up-to-date data – which take into account aging effects or temperature differences, for example – are recorded and the parameters are automatically adjusted. This increases the reproducibility of behavior, full use is made of pump power at all times and the pump status information for further processing on the machine level is as precise as possible.
Travel drive in focus
The Rexroth eOC architecture not only opens up new possibilities in the area of working hydraulics – it also allows a new approach when it comes to the travel drive systems of compact machines. The eOC functions in accordance with the secondary control concept, combining the functionality of a closed-circuit travel drive with the physical layout of an open-circuit drive, which only requires one pump for travel and working functions.
As a result, all travel and working hydraulics functions in compact machines can be combined into one hydraulic circuit – all rotating consumers are connected directly to the pressure line. A secondary logic system with no additional directional valves controls the hydraulic motor’s displacement and output torque to achieve the desired rotational speed. The eOC travel concept requires fewer components in the machine and simplifies the hydraulic architecture.
Complexity in the hydraulic system is moved into the software. Travel direction valves and brake valves are no longer needed. In addition, the combination of working and travel functions in one hydraulic circuit allows the recovery of hydraulic energy during braking or lowering, thus ensuring that the optimum use is made of the drive power.
To learn more about Rexroth’s eOC portfolio, visit www.boschrexroth.com/en/us/transforming-mobile-machines/.
www.boschrexroth.com