www.industry-asia-pacific.com
14
'22
Written on Modified on
Dürr delivers one of the world’s largest RTO installations for Yisheng Petrochemical
Clean exhaust air in chemical production thanks to highly efficient regenerative thermal oxidation.
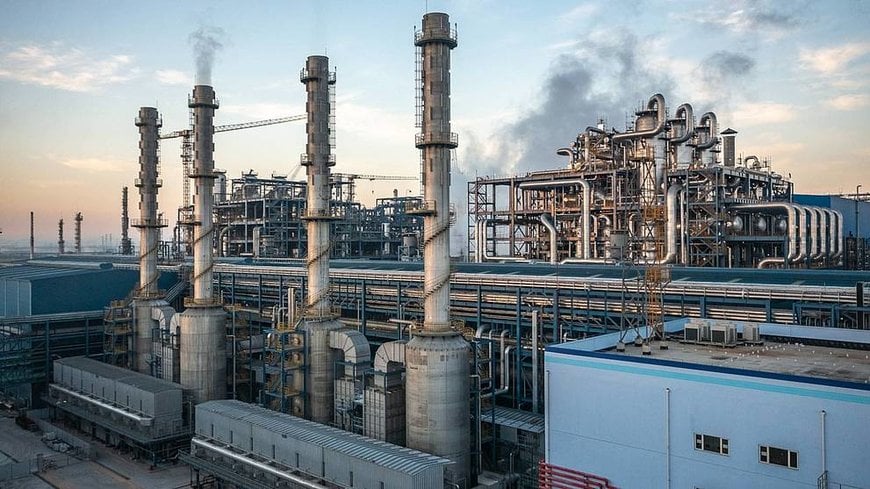
The chemical group Yisheng Petrochemical Co., Ltd. has been relying on air purification technologies from Dürr since 2010. The most recent investment in Eastern China Ningbo/Zhenhai includes a total of seven regenerative thermal air pollution control systems. They ensure reliable, energy-saving and CO2-reduced purification of the polluted exhaust air streams on a large scale. This results in one of the world’s biggest RTO installations with 2.31 Mio. Nm3/h treatment capacity. For Dürr, the project is one of the largest of its kind to date.
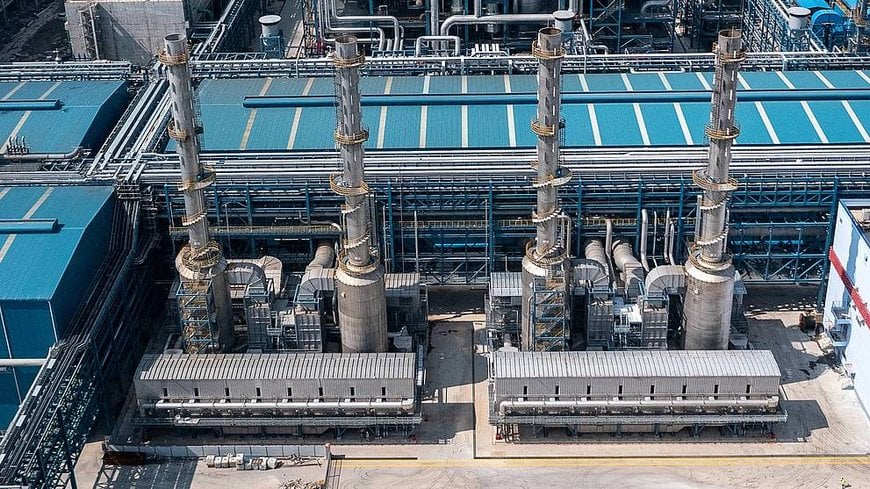
At its site in Ningbo in the Eastern Chinese province of Zhejiang, the chemical group Yisheng Petrochemical Co., Ltd. mainly produces purified terephthalic acid (PTA). PTA is in demand as a starting material for the most important polymer in the plastics industry to produce plastic bottles, textiles and food packaging. Yisheng Petrochemical acts as one of the world's largest PTA manufacturers and production capacities in Ningbo are correspondingly high. The chemical giant's two of seven new production lines each have an output of three million tons of PTA per year. A particular challenge in the production of the colorless powder is the partially polluted exhaust air streams. Dürr was again entrusted to install its Oxi.X RE systems. The systems, which are based on regenerative thermal oxidation (RTO), remove the harmful components from the exhaust air generated during PTA production. This is how Yisheng Petrochemical ensures that no polluted exhaust gases escape into the atmosphere.
Technical excellence for highly effective air pollution control
Dürr supplied seven identical turnkey Oxi.X RE systems for the regenerative thermal oxidation process and a corresponding number of Sorpt.X SW wet scrubbers to Yisheng Petrochemical. Each system consists of a nine-tower Oxi.X RE, a down-stream scrubber and a clean gas stack. The treatment capacity of a nine-tower RTO is about 330.000 Nm3/h, making it one of the world’s biggest RTO installations with 2.31 Mio. Nm3/h treatment capacity for the seven units.
In the units, the exhaust air contaminated with pollutants passes first through a regenerative ceramic heat exchanger. This heats up the exhaust air, which is then very close to the reaction temperature before reaching the combustion chamber. In the RTO combustion chamber, all pollutants are converted into harmless components by exposing them to the suitable combustion temperature. The now purified gases pass again through a ceramic heat exchanger, where they release their heat to the ceramic media. The regenerative cycle is completed.
After the complete oxidation of the volatile organic compounds (VOC) in the RTO units, an acid scrubber removes bromine and other halogenated compounds from the flue gas. Clean air emits to atmosphere at a height of 60 meters through the stack, which is installed on top of the scrubber.
Economical and energy efficient despite large dimensions
Within a few months, four of the RTO units installed at Yisheng Petrochemical were put into operation and have been operating since July 2021, and three additional units were also put into operation in January 2022. A total of 1,340 tons of stainless and carbon steel are used for the RTOs and their ducting, as well as more than 200 poppet valves, over 220,000 pieces of ceramic media, and over 150 kilometers of cable. For Dürr, the project is one of the largest of its kind to date.
All regenerative thermal oxidizer systems made by Dürr achieve a destruction and removal efficiency (DRE) of nearly 100%. This is necessary to meet the more and more stringent emission standards in China and globally. Economic and eco-friendly, Dürr’s RTO systems convince with low maintenance requirements due to sealing-free, horizontally arranged poppet valves and easy access in case an inspection is performed.
Energetically optimized, oxidizers from Dürr can operate without additional fuel and fossil fuel is only needed for the heating-up mode. Self-sustaining with the energy input from the exhaust air, the RTO units contribute to reduce the client’s carbon footprint by operating in auto-thermal mode.
www.durr.com