Bosch Rexroth opens its Customer and Innovation Center in Ulm: Booster for collaborative development in the industry
The Model Factory is an integral part of the Customer and Innovation Center: Bosch Rexroth demonstrates the potential of modular and highly digitalized manufacturing in an area of 500 square meters.
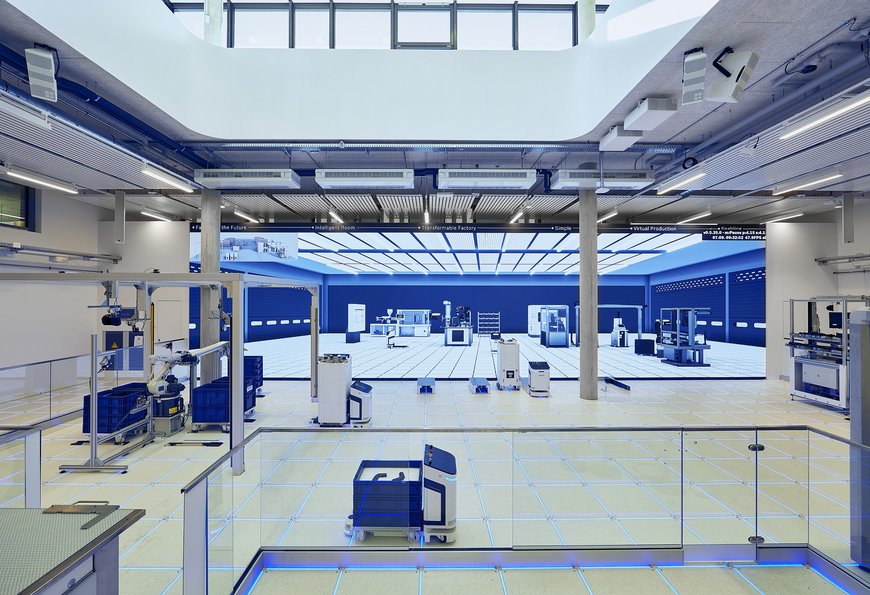
- A Model Factory with real applications shows the Factory of the Future
- Large testing area for mobile machines and events
- Collaborations with customers and partners, as well as internal partnerships, boost innovation
- Carbon-neutral building made from sustainable, regional building materials
Bosch Rexroth opens its Customer and Innovation Center in the Science Park Ulm. The extension, which was initially announced in 2019, is now complete. With the opening of the new center, Bosch Rexroth ramps up its cross-technology development activities and now offers attractive surroundings for customers and employees. The center focuses on factory automation and the electrification of mobile machines. The Ulm center enables Bosch Rexroth to work in close partnership with customers and users, allowing innovations to be experienced, tested and further developed in a Model Factory and in a large outdoor testing area.
“In Ulm, we bring together what belongs together, namely customers and innovations. These innovations are only successful if they solve the challenges of customers — challenges of an economic nature and those relating to the sustainable use of resources,” said Rolf Najork, member of the board of management of Robert Bosch GmbH, responsible for the Industrial Technology business sector and chairman of the executive board of Bosch Rexroth AG.
Primarily software-based products, which allow flexible industrial production and reduce emissions from mobile machines, are developed on-site. The development teams test new products and solutions virtually first and then produce a minimum viable product (MVP), i.e., a basic product that performs the main function but without fully developed detailed functions. Using the MVP, Bosch Rexroth is then able to discuss real applications for the product idea with customers. Based on customer feedback, the MVP is further developed and a prototype is created. Throughout the development process, Bosch Rexroth takes into account customer experience.
“By talking to our customers all the time, we identify their need for innovations reliably and quickly. Our aim is to at least double the number of successful product launches and get the products onto the market more quickly,” said Najork.
The focus: digitalization and electrification
The Model Factory is a key component of the Customer and Innovation Center. Spanning around 500 square meters, it allows Bosch Rexroth to demonstrate the potential for modular, highly digitalized production. Autonomous transport systems for intralogistics, self-learning robots for commissioning and mobile assistance systems with a sensor-supported, virtual protective function are used on a smart floor. The digitalization of all components opens up new opportunities for machine manufacturers and factory operators. A wide range of software functions and evaluable data are the basis for using machines more efficiently in the Factory of the Future. As a result, more and more functions are shifting from hardware to software and being complemented by digital twins. In the Model Factory, Bosch Rexroth can show how machines, systems and even manual workstations can be optimized and converted. With the help of simulations, groundbreaking ideas are tested under realistic conditions, making Ulm’s Model Factory an important Industry 4.0 hub for Bosch.
Other areas of Bosch’s industrial business, such as Bosch Building Technology, Bosch.IO, Bosch Connected Industries and Bosch Engineering and Production Services, can integrate their software and hardware solutions and services and use feedback from customers for further development.
In addition to factory automation, Bosch Rexroth will concentrate on the electrification of mobile machines, such as wheeled loaders and excavators, in Ulm. These machines can be used in agriculture and forestry, on building sites or when handling goods at ports. Because these machines are fully electrified, they are locally emission-free. Bosch Rexroth is thus helping to protect the environment and improve quality of life in cities. To further improve the newly developed electric motors and inverters according to customer requirements, Bosch Rexroth’s Ulm center has a high-performance test stand for electric drives in mobile machines, which offers a peak power of up to 830 kW.
Outdoor area and training rooms for testing and learning
The Customer and Innovation Center, which has more than 8,500 square meters of building space, also includes the TechPark — an outdoor site covering an area of around 10,000 square meters, with workshops and a testing area for electrically driven mobile machines. The TechPark can also be used for outdoor customer events.
Digitalization, connectivity and the IoT will shape work in factories in the long term. Because of this, specialists’ know-how must be able to keep up. With its dedicated Academy, Bosch Rexroth trains employees and customers and gets them ready for Industry 4.0. At the Innovation Center, specialists can learn how to connect machines and workstations and how data can generate added value.
Modern ways of collaborating
Around 200 employees from 18 countries currently work at the Customer and Innovation Center (25% of employees are female developers). By 2022, the number of employees in Ulm is expected to increase to 250. Virtually all positions on-site are connected to electrification, digitalization and software. The Customer and Innovation Center is designed for co-working. Experts from various fields of business, such as mobile hydraulics or electric drive technology, work together with customers in teams made up of specialists from various areas. There are also plans to increase work with start-ups within the Bosch Group and in the greater Ulm area to develop more innovations for customers in a shorter amount of time.
The benefits of a site in the scientific city of Ulm
“We deliberately chose Ulm when we were looking for a location for our Customer and Innovation Center. It offers excellent connections for customers, partners and employees, and its status as a scientific city allows close partnerships between industry and universities, other higher-education institutions and start-ups. Our site in Ulm will therefore provide a further boost for our activities in the area of factory automation,” said Dr. Marc Wucherer, member of the Board of Management at Bosch Rexroth with responsibility for sales. “Even during the construction phase, the close partnership with the City of Ulm and Projektentwicklungsgesellschaft Ulm worked really well. Here in the Science Park, we’re in good company with other innovative firms. This results in innovation clusters that benefit us as a company, our customers and the region as a whole.”
Gunter Czisch, mayor of Ulm, said, “Bosch Rexroth’s Customer and Innovation Center is a highlight in the Science Park. In Ulm, Bosch Rexroth can help to shape the future of factory automation, mobile applications and industrial hydraulics with its innovations. Ulm is also the ideal place for networking: with global customers and the established scientific community in the city.”
Once Projektentwicklungsgesellschaft Ulm (PEG) had refurbished the first Bosch Rexroth building on behalf of the company, it became the developer of the second, newly opened building. PEG’s Managing Director Christian Bried said, “We worked on the project hand in hand with Bosch Rexroth. In spite of the coronavirus pandemic and shortages of materials, we were able to meet Bosch Rexroth’s high demands in regard to the versatility and sustainability of the building. What’s more, we did this on time and within budget.”
Sustainably built and climate-neutral in operation
Bosch Rexroth is committed to sustainability, as well as utilizing regional suppliers and building materials. The wood used in the building’s facade comes from Germany’s Black Forest. The photovoltaic system on the roof supplies the site with renewable energy. The new building is also carbon-neutral, thanks to a combination of district heating and cooling, 70% of which comes from biomass. As a result, the new site is one of over 400 Bosch sites that have become climate-neutral since 2020. The site also has 12 charging stations for electric cars and bikes, encouraging employees and customers to travel in an environmentally friendly manner.
Special labeling for sustainable products
In Ulm, Bosch Rexroth is taking extra steps to stress the sustainability of its products and solutions to its customers. It shows how many products overcome the assumed contradiction between economical goals and sustainability requirements, for example by increasing productivity and using less energy or resources at the same time.
www.boschrexroth.com