www.industry-asia-pacific.com
07
'21
Written on Modified on
25 years of GEA centrifugal bilge water treatment – success story continues after more than 1,000 plants installed with new GEA bilge Separator
The treatment of bilgewater plays a critical role in protecting the oceans. Bilgewater, is a fuel, chemical, oil, lubricant, wash water, soot and pollution "cocktail". To protect the fragile marine ecosystem, bilgewater must be treated before the purified water portion can be returned to the sea.
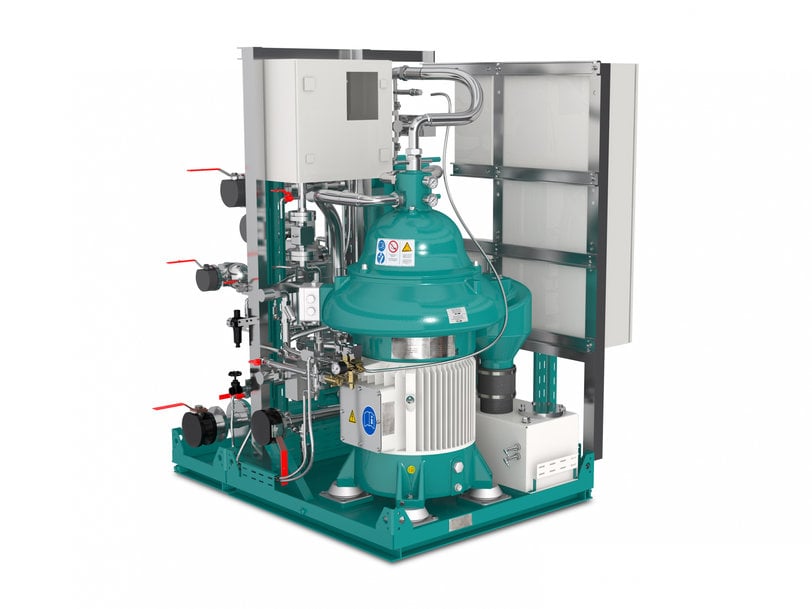
Shipping companies have been using centrifugal bilgewater treatment for decades. This enables them to meet the strict ecological specifications and limit values worldwide, while at the same time benefiting from the economic advantages offered by the system. GEA is now launching the GEA bilge Separator, a new generation of separators with integrated direct drive.
New GEA bilge Separator with impressive key figures
A "GEA bilge Separator family" from 200-5,000 liters in various sizes is offered only by GEA. With its direct drive and best flow rates, the GEA bilge Separator has an efficiency level of 96 percent. It is thus even more efficient than old standard models. Another advantage is the energy saving of up to 30,000 kWh/vessel/year. The space saving is of benefit due to its design with the direct drive. The complete unit has 360° accessibility and a space requirement reduction of 30 percent. The service interval is 16,000 hours, which has been doubled. The time required for maintenance has been reduced by 94 percent. In addition, the system is self-cleaning and designed for unattended operation, eliminating the need for additional personnel. The system drains and cleans fully automatically. GEA separators handle large flow rates with maximum separation efficiency. Vessel movements do not affect the function.
Modular design
GEA bilge Separator systems are modular in design. The main components are feed pump, automatic filter, preheater, self-cleaning centrifugal separator, oil monitor and control panel. They are installed on two modules (feed pump / preheater unit, separator). These modules are assembled into a complete unit and can also be supplied separately. This means that the system can be adapted to local conditions in the best possible way, even where space is limited.
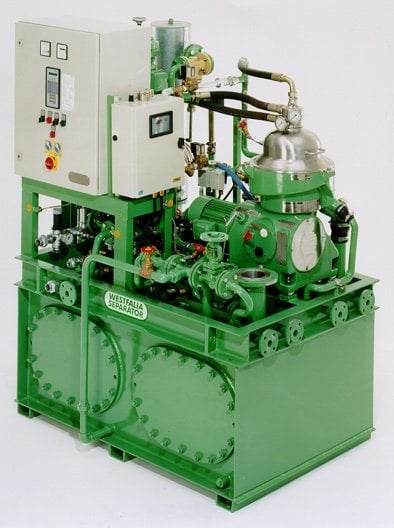
The photo shows a first-generation GEA BilgeMaster.
GEA, shipping companies and the shipping industry working hand in hand for environmental protection and sustainability
It makes a big difference whether bilgewater with a residual oil content of 15 ppm or only 5 ppm is discharged at sea. Equipped with an additional filter, the GEA bilge Separator guarantees a residual oil content of less than 5 ppm in the treated bilgewater and thus contributes significantly to the protection of the oceans.
Better safe than sorry: the GEA SafetyMaster
In addition to the high safety standard of the GEA bilge Separator, GEA offers the SafetyMaster. The system prevents unintentional overboard pumping of bilge water with excessive values by permanently monitoring complete separation. An integrated data recorder stores all bilgewater processing information from the previous eighteen months. All components of the SafetyMaster system are located in a lockable cabinet protected against tampering and installed on the separator.
Competence by tradition
GEA looks back at more than 125 years of experience in separation technology. To date, GEA has installed more than 1,000 machines for centrifugal bilgewater treatment. It is impossible to imagine the global shipping industry without this GEA technology and it has set standards. This has even led to very special "declarations of love". In the Carnival Group, or among cruisers in general, the GEA bilge centrifuge is called "COWS" [Centrifugal Oily Water Separator). The expertise gained has been incorporated into the development of the GEA bilge Separator.
Breakthrough 25 years ago
Exactly a quarter of a century ago, in 1996, a real breakthrough was made in centrifugal bilgewater treatment. GEA experts Dr. Klaus Witte and Klaus P. Lohmeyer were asked by Princess Cruises USA (Carnival) to develop a self-cleaning, centrifugal design for treating bilge water. The shipping company already had the topics of environmental protection and sustainability on its agenda at that time, because bilge water containing oil should not and could not simply be discharged into the sea but required treatment.
GEA's first system had IMO approval MEPC 66(33) 15ppm, today MEPC 107(49) 15ppm. The first system was designed for a capacity of 5,000l/h. With the self-cleaning OSD separator, with flat belt drive, GEA soon offered a BilgeMaster family with different machine sizes and capacities of up to 7,000l/h. Later the generation of OSE separators followed and a small separator for 200 liters, manually cleaning, for installation on yachts.
www.gea.com