www.industry-asia-pacific.com
16
'21
Written on Modified on
Is it time to scale up?
Considerations for manufacturers expanding their operations.
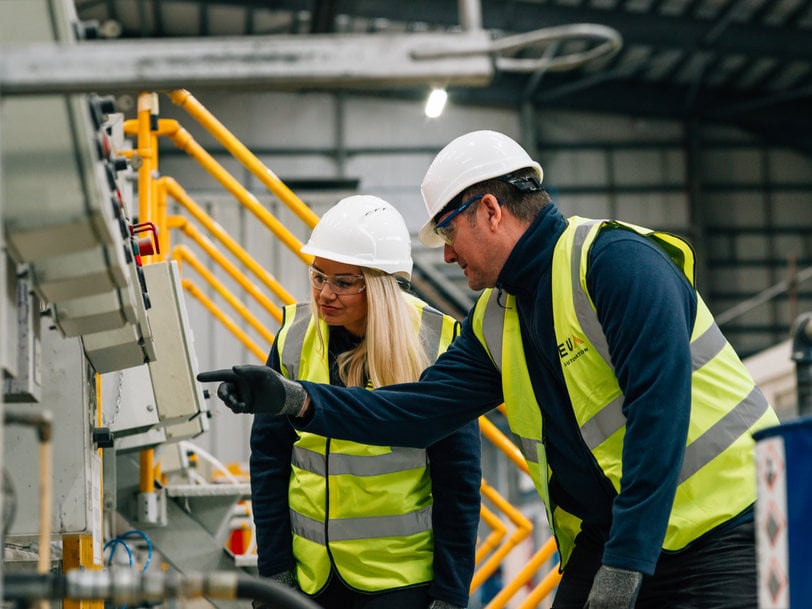
Though small-scale production allows a certain degree of flexibility and customization, scaling up can allow a business to reach new markets on a global level. Implementing automation strategically, along with effective training procedures and quality management can make scaling up a successful way to expand a manufacturers customer base and grow their business. Here, Claudia Jarrett, US country manager at EU Automation, shares guidance for manufacturers hoping to expand their operations.
According to the Small Business Administration, there are around 30.2 million small businesses in the United States alone, comprising over 99% of all businesses and employing 47.5% of Americans. Small businesses have their advantages in manufacturing. They can implement new processes more rapidly and seamlessly respond to changes in demand, and often aren’t subjected to the same regulatory restrictions that larger operations are. However, once a small manufacturer has optimized its products and processes, scaling up the business can offer significant benefits.
Scaling up a small business can be challenging. It requires financial investment, adaptation of existing infrastructure and expanding or retraining the workforce. New equipment may be required to accommodate the increase in production. It is also important that quality and consistency are maintained on a larger scale.
EU Automation began as a small business around 10 years ago and has since established a global reputation as a leading supplier of parts and service in industrial automation. Catering to 20,000 customers across 163 different countries, EU Automation is an example of how, with strategic planning, manufacturers can scale up their operations for long-term sustainable growth. Here are three key considerations for entrepreneurs on how this can be done.
Training
Training is an essential aspect when it comes to scaling up an operation. Knowledge and expertise are often specific to individuals within the business. To scale up, ownership of these skills should instead lie with the business itself — made possible through a training procedure.
A comprehensive and formalized training process can help to standardize processes and procedures in a way that can be carried out by all employees. This can also protect a business against the loss of key employees and increase efficiency. If standard procedures are implemented, operations are not reliant on the availability or skillset of an individual but can be carried out by workers at all levels.
Quality
Maintaining the integrity and quality of your original product is essential when scaling up an operation. This is often a challenge when making the change to large-batch production due to the many variables involved. Scaling up production processes that require additional finishing or post-processing, such as 3D printing, can actually make quality assurance more labor-intensive, as the quality of each step must be checked. Manufacturers must consider effective ways to maintain quality when increasing output without also significantly increasing the additional work needed to achieve this.
Sacrificing quality can impact the business as a whole. Reputational damage and correcting these issues can be costly, along with fines and compensation for late delivery or faulty products. It can also cause lasting damage to customer loyalty and business reputation, leading to loss of opportunities at a time when they are crucial for growth.
Automated quality assurance solutions can help to ensure consistent quality of output at high volumes. Autonomous machine vision systems can offer manufacturers a low-cost and flexible solution to assess quality at any point in the production process. They also require minimal training to operate, removing the need to bring in external expertise to optimise quality assurance.
Automation
Introducing automation solutions can be a daunting venture for a small manufacturing operation, and does require time and investment to implement them effectively. However, manufacturers can reap the benefits of automation by using simple and cost-effective solutions to effectively meet demand and increase efficiency.
Many manufacturing processes can be automated easily using collaborative robots, or cobots. They are simple to set up and versatile, able to automate a range of existing tasks. Plus, automation does not necessarily require large amounts of floor space; many available robots are compact and lightweight, able to easily integrate into existing infrastructure.
Programming robots does not need to be complicated either, many available solutions are easy to programme and can require little to no prior experience. Automation software is often intuitive and requires minimal training.
Smart sensors are another option for upgrading operations, and they can be retrofitted to existing machinery for a cost-effective solution. When scaling up, machines may be used more intensively and more frequently, making maintenance more important than ever. The sensors monitor machine condition and gather data for fine-tuning performance and predictive maintenance. This can reduce failure rates and prolong the life of the equipment, minimising costs and facilitating increased production.
Scaling up small manufacturing businesses brings many challenges. However, with effective training procedures, comprehensive quality assurance and strategic use of automation solutions, scaling up can bring long-term sustainable growth and success.
Scaling up and implementing automated processes doesn’t have to be costly or complicated. EU Automation supplies new, reconditioned, and obsolete automation parts worldwide. Its global network can offer parts and services to reduce downtime, save on costs and support automation and scaling up.
www.euautomation.com