www.industry-asia-pacific.com
13
'21
Written on Modified on
GEA marine Separator prime sets new standards in separation technology with higher efficiency
"Better is the enemy of good" - this quote by Voltaire applies without any ifs and buts to an innovation of the machine and plant manufacturer and solution provider GEA.
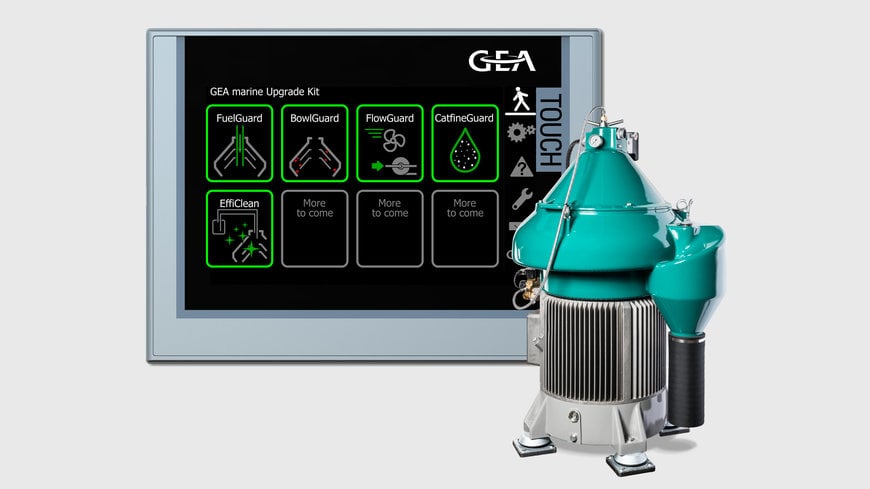
The GEA marine Separator prime with Upgrade Kit is the consistent further development of the GEA OSE Separator. Based on the CWA 15375 standard, the GEA marine Separator sets new standards in separation efficiency, offers the best certified flow rates (CFR) on the market and is tailored exactly to the dimensions of your machines. With the current generation of centrifuges with integrated direct drive, ship operators are heading directly into a future that will be even more economical, requires less maintenance and saves space on board thanks to the GEA marine Separator prime.
GEA separators for economical operation of marine engines
GEA centrifugal separators specialize in fuel and lube oil treatment, bilge water treatment and sludge removal in marine applications. With their high accelerating power, the separators ensure reliable performance and economical operation of marine engines and increase service life even under extreme conditions.
Direct drive now leads into the future
The GEA marine Separator with integrated direct drive represents the latest generation of separators with its characteristics of saving energy and reducing the carbon footprint. The market has already accepted the innovation very well. With the direct drive, the GEA marine Separator does not require a conventional separate motor, belt or clutch. Only after 16,000 operating hours or after two years the drive unit is replaced by a GEA OEM certified exchange unit with full new warranty.
One of the biggest advantages for all ship operators is that, for the first time, the spindle and motor are available as a compact plug-and-play exchange drive unit - making maintenance of the separator very easy. Thanks to the efficiency of the drive and the absence of belts, almost all the energy is transferred directly to the bowl. This saves up to 30,000 kWh per year and ensures sustainability.
The future of marine is digital
With the GEA marine Upgrade Kit, GEA automates the functionality of its separators for marine applications. For GEA customers, this means optimized operation of their plants, an improved carbon footprint and realized cost savings. The Upgrade Kit is available as a retrofit solution for OSC, OSD and OSE separators.
For new vessels, the GEA marine Separator prime is the right choice. The Upgrade Kit is already included in the scope of the prime line.
The new GEA marine Upgrade Kit digitizes several processes in parallel. Five so-called "Guards" monitor and control important functions. Specifically, these are FuelGuard - automated reduction of fuel losses, BowlGuard - clever solution for avoiding high disposal costs, FlowGuard - fuel treatment on demand, CatfineGuard - finest fuel at the push of a button, and EffiClean - best CIP cleaning.
Further Guards for even more customer benefits
GEA, the company announced, will consistently continue to work on the development of digital functionalities of its separators. A key focus is to make GEA customers' process operations ever more sustainable and efficient. GEA plants are helping to reduce CO2 emissions worldwide, making a vital contribution to marine conservation and a sustainable future.
www.gea.com