www.industry-asia-pacific.com
15
'21
Written on Modified on
The Exoskeletons Are Here
While the use of exoskeletons in industry is still at the lower end of the spectrum, there is growing awareness about the benefits of exoskeletons in industrial applications.
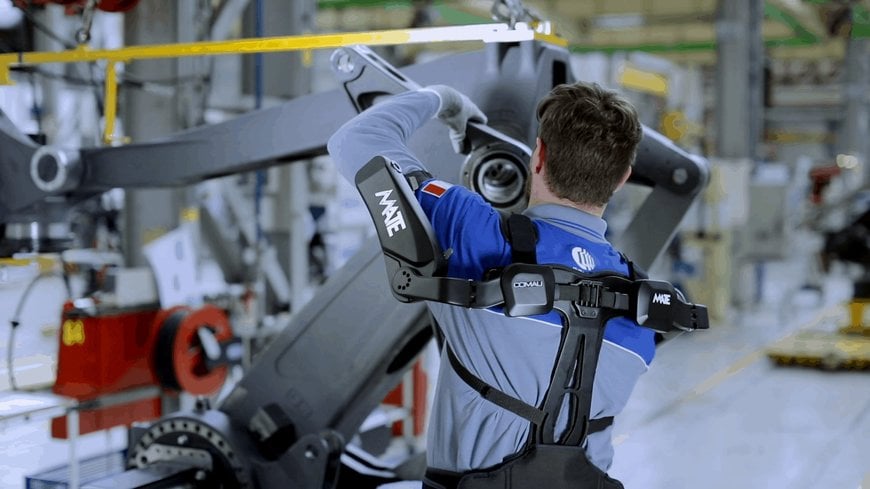
In nature, some animals and insects have exoskeletons or external skeletons unlike most other living creatures, including humans, who have internal skeletons or endoskeletons. Crabs, lobsters, cockroaches, grasshoppers and several types of beetles are examples of natural exoskeletons. The early body armour adopted by human beings for combat was inspired by these exoskeletal creatures. The exoskeleton as a wearable device to augment human capabilities is of more recent origin, even as the idea was considered by many early inventors. An early example is a passive spring body brace invented in 1890, which supported the upper body in a stooping position, to relieve fatigue. However, the concept received serious attention only in the 1960s when GE developed the Hardiman in collaboration with the US Army and Navy for military use. Though the project was not successful, it paved the way for further development of the concept.
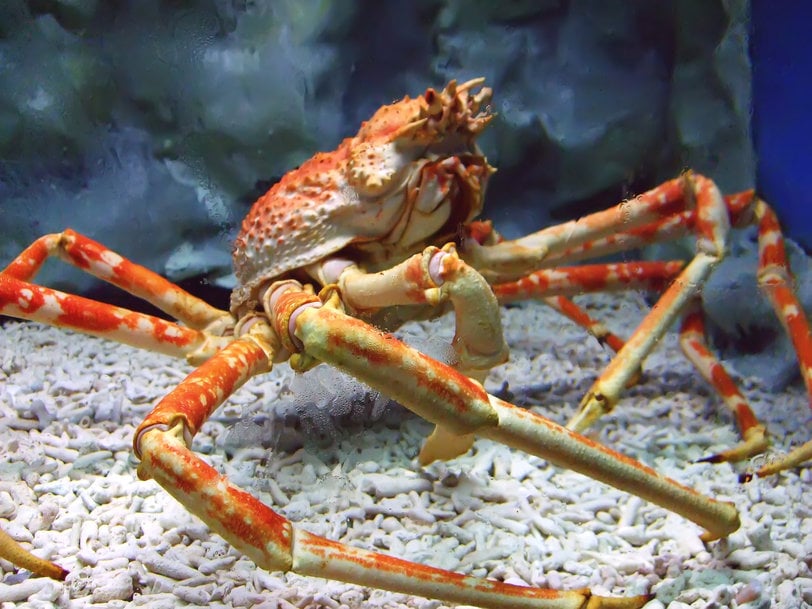
Example of a natural exoskeleton – the Japanese Spider Crab.
Modern exoskeletons, developed mostly during the last two decades, are of two types – active and passive. Active exoskeletons are equipped with sensors and actuators, and powered by battery operated electric motors, pneumatics, hydraulics, or a combination of these systems. Passive exoskeletons are purely mechanical devices and use the restorative forces of elements like springs and dampers. There are further divisions in exoskeletons based on form – upper body, lower body or full body exoskeletons. Based on applications, exoskeletons are divided into two broad categories – medical and industrial. Medical exoskeletons are used in the rehabilitation of patients post-surgery or to assist in those recuperating from paralysis or muscular dystrophy and other disabilities. Industrial exoskeletons also have military applications – in fact these were initially used in defence services and more recently have been deployed in industry. Exoskeletons are variously called exosuits or wearable robots, but unlike robots, which are autonomous and work independent of human support, the exoskeleton works in tandem with the human body, not as a replacement for any limb.
This article is basically about industrial exoskeletons used by workers engaged in various activities. In spite of mechanisation and automation of workplaces with various handling equipment like trolleys, hoists, pallet trucks and overhead cranes, there are a lot of activities in industry, which are physically demanding yet cannot be automated. These vary from lifting of heavy loads or working in assembly operations that involve working long hours in standing or bending positions. Also many assembly operations in automotive and aerospace industries involve workers engaged in tasks with their arms continuously stretched upwards, carrying heavy tools. These activities cause pressure on the lumbar spine and/or on muscles in various parts of the body, which in turn result in work related musculoskeletal disorders or WRMSDs.
Growing health concerns
Across the developed world – the Americas, Europe, Japan and now even China – the population is ageing and so is the working class – people working in factories and utilities – the typical blue collar jobs where manual labour in various forms is routine. These are also the jobs where the risks of workplace injuries, often of serious nature, are high and WRMSDs are common, adding to the overheads in terms of productivity loss due to sickness and absenteeism as well as high insurance costs. Apart from the unfairness of letting ageing employees go, there is that matter of the younger generation not so enthusiastic about jobs in factories and anything that involves physical activity. The situation is ripe for the induction of exoskeletons on the shop floor.
According to a discussion paper published by the European Agency for Safety and Health at Work, over 40% of workers in Europe suffer from lower back pain or shoulder complaints. Furthermore, 63% of workers perform repetitive tasks or frequently work (46%) in potentially hazardous positions. This not only results in injuries and absenteeism, but also costs about 2% of the gross domestic product of the European Union. Across the Atlantic in the US, the Centers for Disease Control and Prevention states that back pain is the most prevalent work-related health problem. The Occupational Safety and Health Administration estimates that employers pay nearly $1 billion for direct workers’ compensation. Against this backdrop industrial exoskeletons are becoming popular to address the many concerns of worker safety and productivity.
The potential benefits of industrial exoskeletons are many, as these are designed to ease the load on the spine, decrease muscle activity and improve the posture, reducing the risk of injuries. Upper body exoskeletons reduce shoulder discomfort and increase productivity in assembly operations. While the use of exoskeletons in industry is still at the lower end of the spectrum, there is growing awareness about the benefits of exoskeletons in industrial applications, especially in automotive, construction, manufacturing and logistics sectors.
An expanding market
According to a recent analysis by Frost & Sullivan, the global industrial exoskeletons market is expanding rapidly, driven by high injury costs and aging and shrinking skilled workforces across sectors. It is estimated to witness nearly a seven-fold growth, reaching US$426.6 million by 2025 from US$62.7 million in 2020, up at a compound annual growth rate (CAGR) of 46.7%. (These figures do not include medical or military exoskeletons, only industrial ones.)
“Manufacturers are investing in R&D to develop technologically advanced exoskeletons, which improve performance and productivity,” says Anjan Roy, Chemicals, Materials & Nutrition Research Analyst at Frost & Sullivan. “To deploy the latest innovations, manufacturers will focus on the robot-as-a-service (RaaS) model to improve affordability for end users and test products for large-scale deployment.”
Among the end-use industries, manufacturing – driven by the automotive sector – held the highest revenue share in 2020 and is projected to top US$271.4 million in 2025. Other manual, labour-intensive industries such as construction and transport will also make extensive deployments of industrial exoskeletons over the next four to five years as companies across these sectors focus on reducing the cost of on-the-job injuries. “From a product segment perspective, active or powered industrial exoskeletons – which are technologically advanced PPE that are powered by batteries or electricity – are expected to have the highest revenue share at 69.9% over the forecast period, whereas passive industrial exoskeletons will constitute 30.1% market share,” adds Roy.
Industrial exoskeletons in the market
When the Swiss startup noonee launched its prototype Chairless Chair in 2014, German automaker Audi AG was one the first to test the wearable seating passive exoskeleton at its assembly lines at Neckarsulm plant. “With the use of the Chairless Chair, we are continuously improving ergonomics in assembly operations. We also anticipate new applications for colleagues with reduced physical capabilities,” Dr Mathias Keil, Head of Industrial Engineering Methods at AUDI AG, had then stated about the experiment. More automakers have since adopted the ‘Chair-olution’ as noonee called its invention, and it has undergone many refinements since. “Through active sitting on the Chairless Chair, your back and thigh muscles are strengthened while your spine, intervertebral discs and knees are relieved. The Chairless Chair supports a healthy and upright sitting posture and takes preventive action so that pain does not occur at all,” claims the company in its latest flyer made available during the presentation at the Digital Hannover Messe 2021. The new Chairless Chair 2.0 is a passive exoskeleton that allows workers to change easily between sitting, walking and standing.
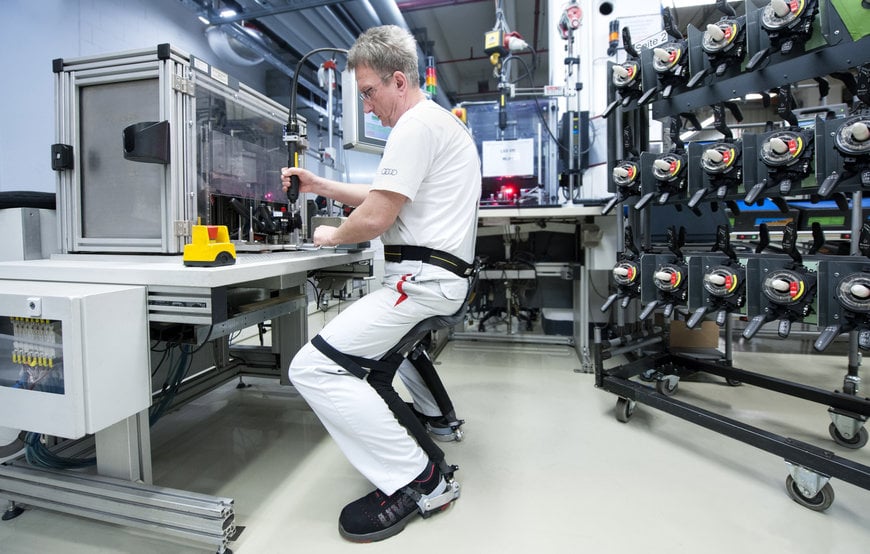
Swiss startup noonee’s Chairless Chair tested extensively by Audi AG.
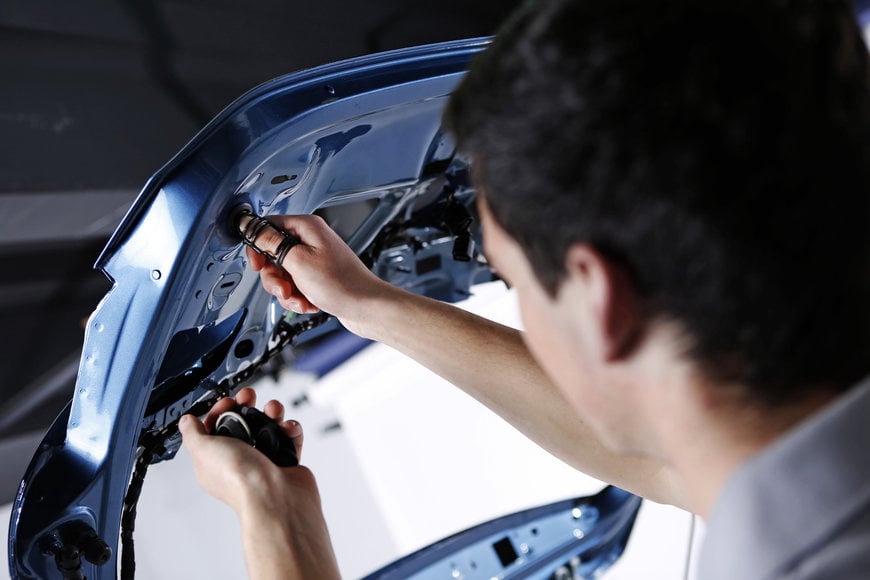
The Paexo Thumb exoskeleton protects the tip of the thumb.
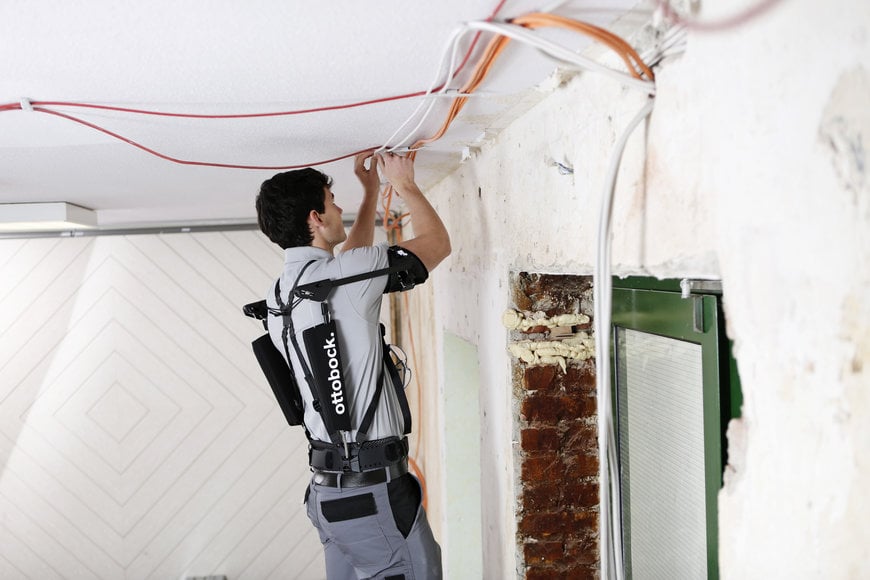
Ottoblock designs and manufactures the Paexo range of exoskeletons.
At the 2019 Hannover Messe, German Bionic, a robotics company, presented the first connected robot exoskeleton compatible with IIoT. The Cray X exoskeleton, having undergone many improvements, is said to be the first cloud connected exoskeleton, enabling complete integration into Smart Factory and Industry 4.0 environments.
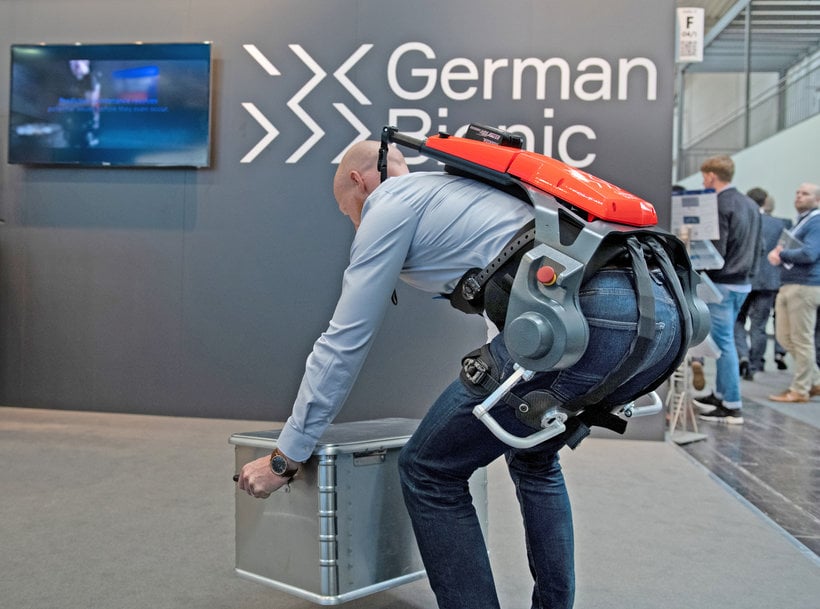
The Cray X exoskeleton from German Bionic, at Hannover Messe 2019.
Skelex, a Dutch startup, is another company that has successfully introduced an upper body passive skeleton in the market, primarily for the aerospace and automotive industries. Gaurav Genani, an engineer by day is a guitarist after work, performing in a band and nursing a wrist injury, apart from having gait issues not uncommon with guitar players. While doing his master’s thesis on musculoskeletal disorders amongst musicians at TU Delft in Rotterdam, Gaurav had his Eureka moment that led to exoskeletons and the founding of Skelex. What started as an idea in 2013 finally found its way to the market in 2017 as Skelex 360, with Airbus Industrie among its first customers. The Skelex exoskeleton is powered by the proprietary FlexFrame Technology, the device adapting to the user’s body shape, and supporting biological movement of the shoulder joint, transferring the weight to the lower body. Skelex however does not manufacture these exoskeletons, preferring to concentrate on design and innovation, and has outsourced manufacturing to another Dutch company.
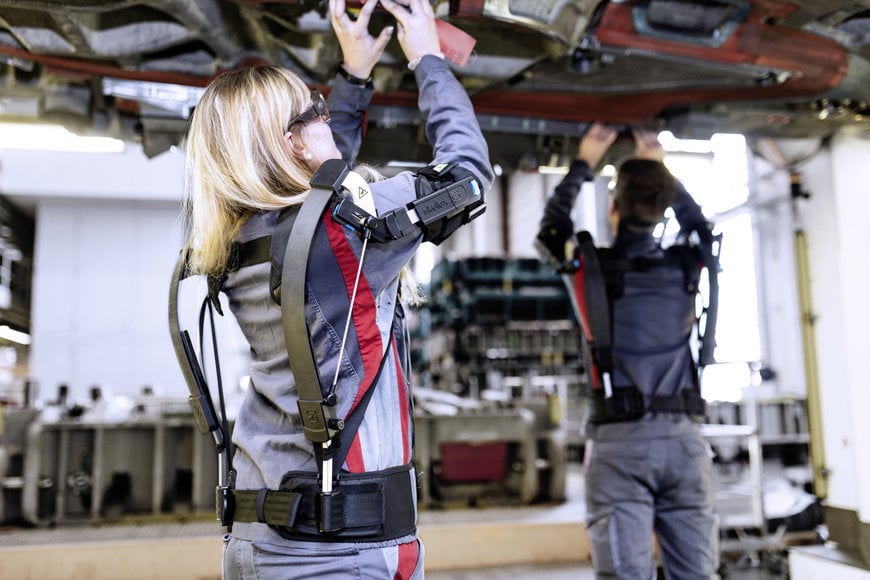
The Skelex exoskeleton is powered by FlexFrame Technology.
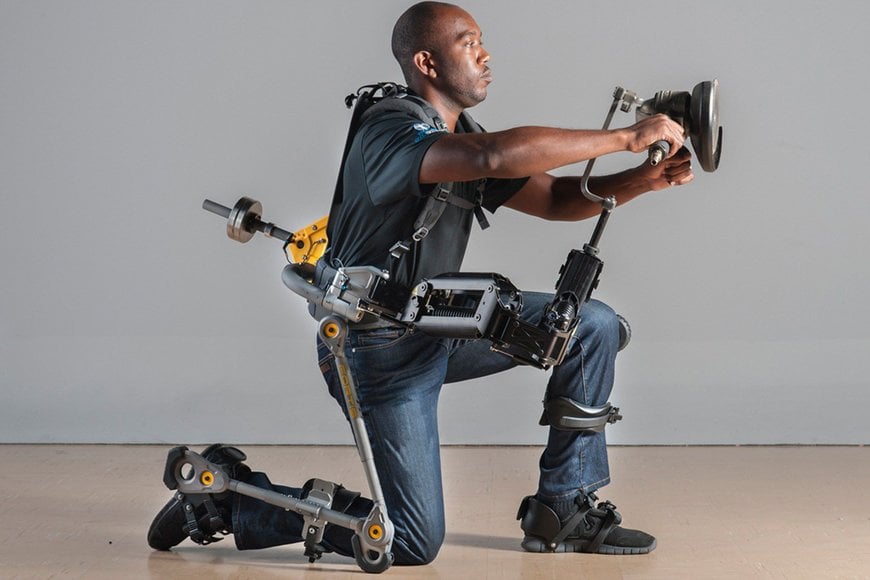
The FORTIS from Lockheed Martin is suitable for handling heavy tools.
Korean company Hyundai Motor Group is also engaged in research and development of exoskeletons as part of its robotics project. Hyundai’s latest exoskeleton wearable robot, Vest Exoskeleton (VEX), has won the Product Design category (Innovative Product field) at the Red Dot Design Awards, the prestigious international design competition. VEX was developed in line with Hyundai Motor Group’s commitment to the health and safety of its industrial workers. It is designed to prevent injuries while advancing the field of robotics. The compact design is achieved using the latest technology that eliminates the need for a battery. VEX, which wears like a backpack, utilises a polycentric axis to provide a maximum force of 5.5 kgf – an astonishing achievement given it weighs only 2.8 kg. In addition to VEX, Hyundai has also designed another lightweight wearable robot, the Chairless Exoskeleton (CEX). With CEX, workers can easily maintain a sitting position without a stool or chair.
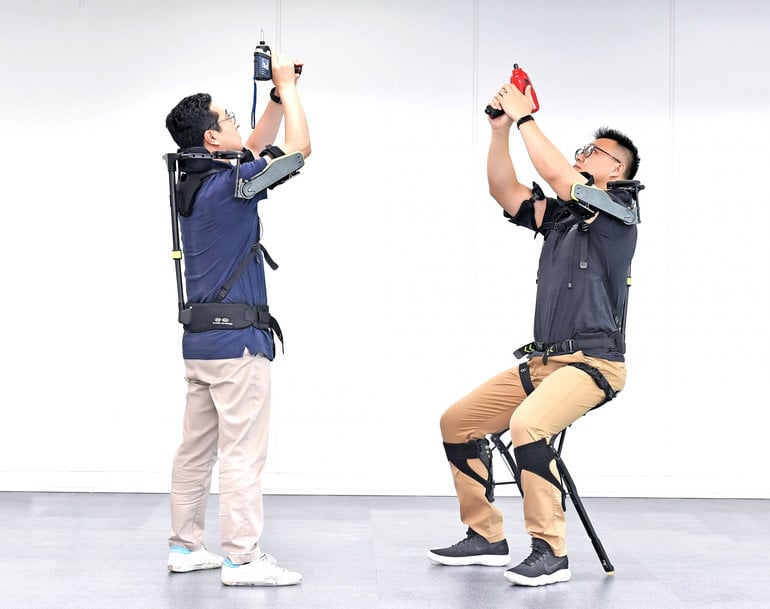
Hyundai Motor Group’s VEX and CEX exoskeletons.
No article on exoskeletons can ignore the contribution of Dr Homayoon Kazerooni, academician and entrepreneur. A professor in the Mechanical Engineering Department at the University of California, Berkeley, Dr Kazerooni is also the director of Berkeley Robotics and Human Engineering Laboratory. The laboratory’s mission is to develop fundamental scientific and engineering principles on robotics, control sciences, exoskeletons, and bioengineering. Dr Kazerooni founded Ekso Bionics which became a public company in 2014, and is the founder and current CEO of US Bionics (DBA suitX), which brings advanced exoskeleton technologies to various markets. Most of the technologies developed in this lab at Berkeley have found their way to market. In fact, suitX offers all three individual exoskeleton modules designed to be able to work in unison to assist the shoulders, back and legs. Each module can be worn individually or in combination to make seven different configurations to cater to customers' specific needs.
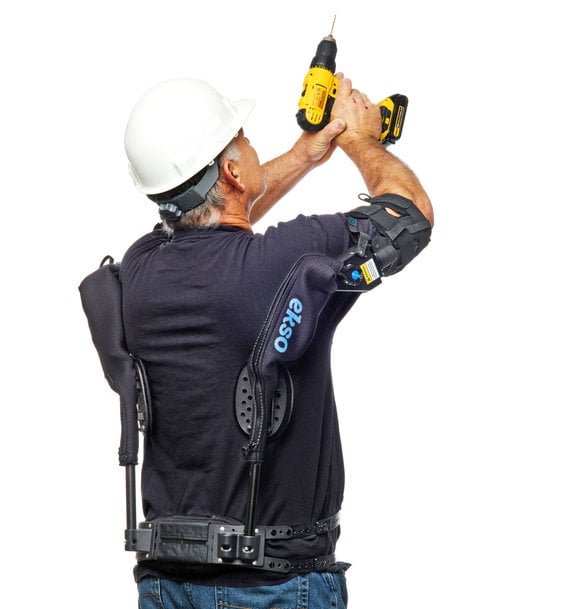
The exoskeletons have arrived and are in use across various manufacturing sites and assembly operations globally. These are getting better and lighter with new materials like ultralight carbon and soft, super strong technical textiles used in their construction. Once prohibitively expensive, exoskeletons are now within the affordable range of large companies, and with growing popularity and mass production, prices are expected to fall further. But it is still early days and the jury is out on the safety and efficacy of the exoskeleton. In the absence of empirical evidence based on detailed studies as well as absence of standards, there are concerns expressed about the health and safety aspects. For example, the US Consumer Product Safety Commission (CPSC) has warned that muscle strain could occur if a powered exoskeleton moves beyond the normal range of motion of a user’s joint. There is also the risk of skin irritation or chemical burns if an exoskeleton battery leaks corrosive materials. A study has pointed out that some upper body exoskeletons do not reduce the total load on the worker, merely shift it from the shoulders to the lower back and legs. Other risks include pressure wounds or compressed nerves from prolonged use. When such wearable devices are used by multiple users, poor hygiene could spread infectious diseases.
In 2017, ASTM International, the international standards organisation, proposed a guide to provide standardised tools to assess and improve the usability and usefulness of exoskeletons. Accordingly the ASTM Committee F48 was formed to develop voluntary consensus standards for exoskeletons and exosuits. It is currently working on the proposed standard, WK68719, working through six subcommittees that include about 150 members, including startups, government agencies, and enterprises such as Boeing and BMW. The F48 committee has already published the first two standards regarding terminology and Standard Practice for Labelling and Information for Exoskeletons, many others are under development. In February 2021, the committee approved a new standard to help establish ergonomic parameters and test metrics. According to ASTM International board member Christopher Reid, the new standard can be used during the iterative design process of exoskeleton creation as well as for comparisons between commercially off-the-shelf ready systems. It is a work in progress and the standards are still evolving. But the exoskeleton has arrived.