www.industry-asia-pacific.com
23
'20
Written on Modified on
Becoming a master of all trades
Diversification will help manufacturers navigate the unpredictable COVID-19 markets.
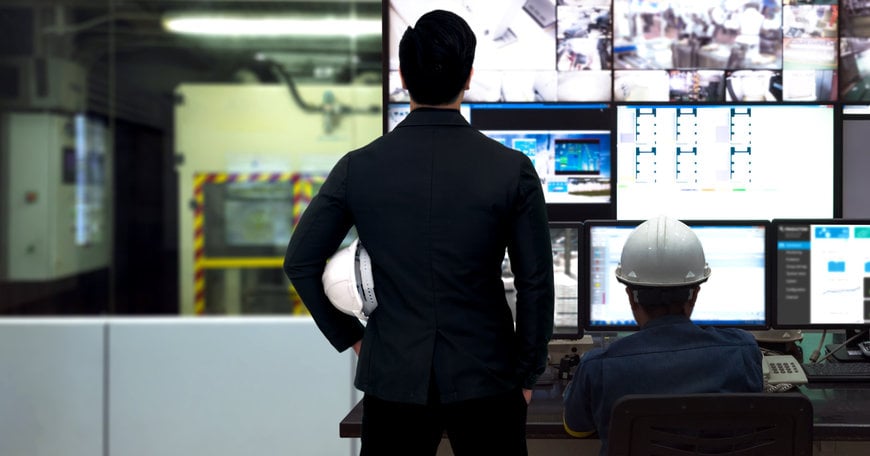
“You must be diversified enough to survive bad times, so that skill and good process can have the chance to pay off in the long-term,” said American academic and investor Joel Greenblatt. This is certainly true for companies that are branching out into new sectors to overcome the uncertainties of COVID-19, while other manufacturers are falling behind. Here, Claudia Jarrett, US country manager at automation parts supplier EU Automation, explains how software is giving some businesses the edge.
The advantages for Industry 4.0 technology are well-know. From improved productivity and operational savings, to increased collaborative working and better experiences for the end customer, it’s a no-brainer. Despite this, the roll-out of digitalized processes is still low among manufacturers in 2020, according to IoT Analytics’ latest Industry 4.0 & Smart Manufacturing Adoption Report.
Less than 30 per cent of manufacturers say they have extensively adopted these new technologies; although North American manufacturers were revealed to be the greatest adopters of the Industrial Internet of Things (IIoT). Unsurprisingly, automotive manufacturers — always the leading innovators when it comes to any new form of technology — were revealed to be the most digitalized sector. Yet, despite these advancements, why is there still so much reluctance to digitalize?
There are a number or reasons. One is that manufacturers assume that integrating Industry 4.0 will be expensive — a wrong assumption, as we’ll examine below. Other companies are set in their ways and see no reason to upgrade their existing machining setups. And, there are manufacturers that are simply unsure as to how modern, digitalized processes can fit into their existing ways of doing things.
Manufacturers will need to put these hesitancies to one side in the era of COVID-19. In its recent COVID-19: Briefing note, analyst McKinsey & Company describes the upcoming climate for manufacturers as the “next normal”, characterized by unpredictable high or low demand scenarios. The report says that resilience will be needed if manufacturers are to navigate an economically and socially viable path.
This is confirmed in Pricewaterhouse Coopers’ (PwC) report, COVID-19: What it means for industrial manufacturing. PwC recommends that companies expand into new industries, and take advantage of fresh revenue streams, to sidestep defunct markets and fully embrace new opportunities. In other words, diversification.
So, machine shops that once specialized in a particular are, like automotive, are branching out into new areas. Defence, aerospace, oil and gas or commercial applications are all examples. In a practical sense, this means introducing all kinds of tough-to-machine materials to their CNC lathes and mills — aluminum one day, hard non-alloyed steels the next — with the utmost productivity and machine utilization.
Savvy machine shops know that best way to achieve this is through Industry 4.0. That is, consolidating multiple machines under a centralized Enterprise Resource Planning (ERP) system with Human Machine Interfaces (HMIs), which can handle these material changeovers and unfamiliar components.
But how can manufacturers outside of IoT Analytics’ 30 per cent — those that are wary or unwilling to embrace the IIoT — get onboard?
As easy as CNC
It is completely understandable that many manufacturers are wary of how Industry 4.0 technologies can integrate into their existing setup and systems. Yet, a quote by Machiavelli, the father of modern political philosophy, comes to mind: ”Whosoever desires constant success must change his conduct with the times.”
Digitalization is, therefore, a balancing act of sorts. Let’s focus on multi-axis CNC machines for a moment. Generally speaking, a key signifier of growth for machine shops is acquiring more machines. This goes hand-in-hand with successful diversification, as does purchasing machines with wider range of capabilities. CNC machines with full five-axis capabilities, or multifunctional machines, bring more processes into one station to process a wider variety of tough materials like aluminum or unalloyed steels.
The next step is to control these machines through a centralized ERP to ensure the overall production setup runs smoothly, while machine utilization is optimized to the fullest. The challenge here is that the manufacturer might operate dozens of machines from different makers that were manufactured years apart, each with their own way of working. How can machine shops bring all these systems together, cost-effectively, and without compromising their existing processes?
Soft approach
One solution is through the use of software, upon which manufacturers and machinists around the world are becoming more heavily reliant on each year.
Popular examples include Sandvik Coromant’s CoroPlus® Machining Insights platform, a Cloud-based platform that is designed to give manufacturers greater visibility of CNC machine tools and machining processes. Any easy-to-use HMI allows operators to analyze, identify, and eliminate common sources of downtime and inefficiency. the tool can also integrate seamlessly into existing ERP systems.
Or, there is the Mitutoyo’s MeasurLink® data management software system. According to one case study, a manufacturer of automotive brakes was able to capture and supply real-time accurate historical data up to ten-times faster with the system. The end result was that the manufacture was able to maximize production and minimize metallurgical defects in the components it produced.
There is an example of how software can directly benefit Quality Management Systems (QMSs), and help manufacturers win accreditations like the ISO 9001:2015, or the AS 9100 quality standard for aerospace. Both standards have proven essential for manufacturers seeking to diversify, and win contracts, in new sectors.
With these system in place, machine shops can address the practicalities of running a wider variety of challenging materials through their CNC lathes and machines. In doing so, to quote Greenblatt, they can be “diversified enough to survive bad times, so that skill and good process can have the chance to pay off in the long term” — despite the challenging and unpredictable times ahead.
www.euautomation.com