www.industry-asia-pacific.com
15
'20
Written on Modified on
Reliability and Productivity: The Foundation of Automated Warehouses
The logistics and warehousing industry has been undergoing a period of immense change, most notably in recent months due to the coronavirus pandemic.
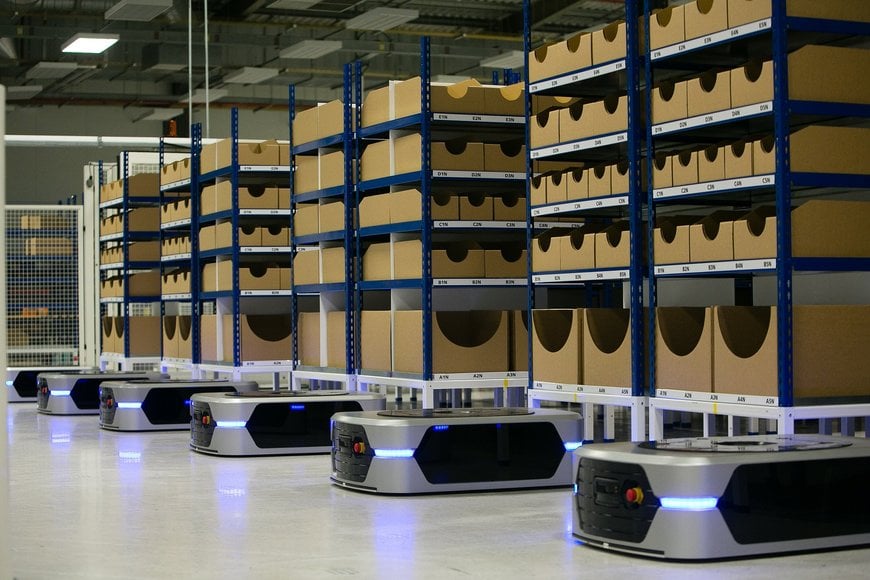
Demand for online deliveries has gone skyward, and retailers have had to adapt rapidly. Customers are shopping online all over the world and automation is becoming fundamental to the warehousing and logistics industry - particularly for online retail products sold in volume.
What type of automation is used in warehouses?
Automated warehouses are efficient, fast, flexible and reliable. They allow for improved warehousing, goods distribution, and optimum material flow. An automated warehouse uses a few key pieces of technology, such as an automated storage and retrieval system, which consists of a variety of computer-controlled systems for automatically placing and retrieving loads from defined storage locations. Central to these systems are the components that guide and transfer a component around the system. Whether it’s a linear actuator to vertically retrieve a part from high racking or a ring system to rotate an autonomous picking robot, linear and rotary products play a key part.
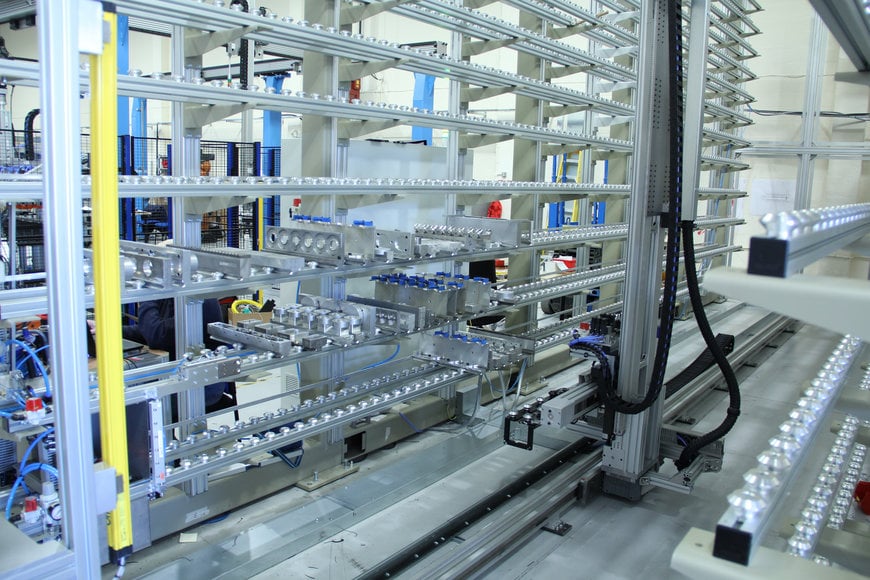
Automated Storage Systems; think vertical
As with nearly every industry, space is a premium and a key benefit of an automated warehouse is its utilisation of space. Only a small footprint is needed as space is used in a vertical capacity, with high rackings going up to the ceiling. Whereas pick and place operators are limited by their height to reach products un-aided, automated storage and retrieval systems are limited only by the size of the system designed, thereby increasing the storage capacity. Whether it’s a rack driven system transporting boxes vertically or a robot climbing shelves to collect orders, space maximisation is easily achieved.
Indeed, one of the global leading online retailers use HepcoMotion’s DLS4 belt driven linear actuators to vertically transfer products through a food filling station. Comprising belt-driven linear modules, an AC motor/inverter package and a range of compact planetary gearboxes for use with servomotors, Hepco’s DLS4 saves hours in design and specifying time. Here, a belt driven carriage unit vertically transports boxes up to a height of 4 metres to transfer a product, and then back down again. This process is repeated up to 300 times an hour. Working with food items and a required operating temperature of between -5° to +40°, this is a challenging environment requiring a corrosion resistant actuator; Hepco’s corrosion resistant DLS4 (CRDLS4) was specified. A high duty application, with longevity of utmost importance, Hepco is able to provide an impressive 10 year life span for this application.

This system required a height of 4m, but any desired height can be achieved with the DLS4s. Hepco’s DLS4 are supplied in sections in any length to 8m as standard, and can be butted together to the required height. Any size warehouse space can therefore be accommodated, ensuring space is maximised. The system can also easily grow in a modular way – a key benefit to ensure future-proofing.
Automated Storage Systems; think modular
Traditional static warehouse solutions can struggle to cope with the changing needs of the industry. Scalability, adaptability and flexibility are at the very core of Dublin-based Eiratech Robotics, innovators of a mobile goods-to-person robotics automation platform. In the Eiratech warehouse environment, autonomously guided vehicles (Eirabots), operated via a wireless network, bring racks containing the required product to the picking station where the product is picked and packed. Minimal infrastructure is required; the system can be easily installed, extended and moved.
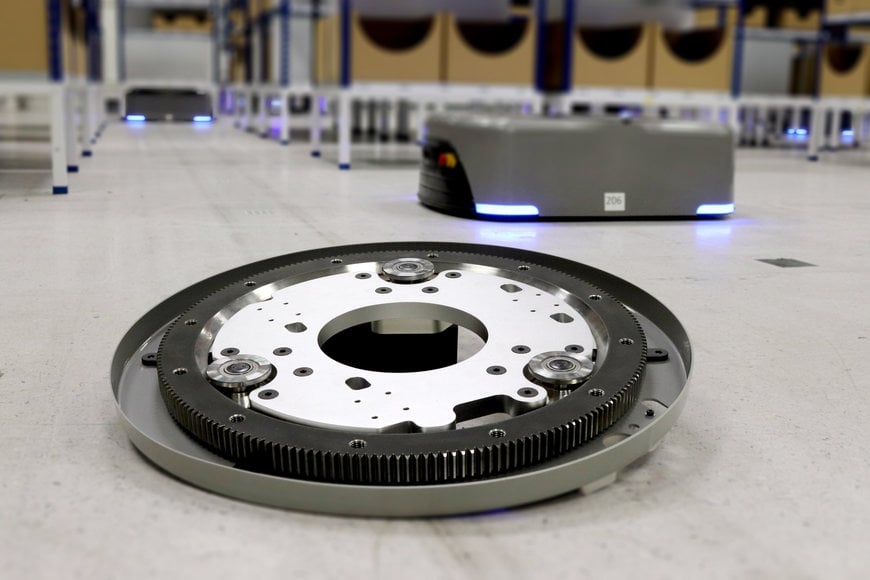
At the centre of the system (quite literally!) is Hepco’s heavy duty ring guide. The HD ring is used on the turntable of the robot to rotate the robot in different directions. Specified to handle millions of rotations in its lifetime and the ability to work with axial loads up to 700kg, the ring also has to manage radial and moment loads in order to accelerate and decelerate a top-heavy rack. A slewing ring could not be used as an open centre was needed to enable a camera to read a barcode placed on the underside of the payloads. Having worked together before, HepcoMotion was the first choice for Eiratech. A custom HepcoMotion HD ring was used, with a bespoke outer gear. Maximising efficiency and improving accuracy, Eiratech offers an enticing automated solution for warehouses.
Reliably reliable
With the focus on speed and consistency to achieve quick orders, reliability of components is crucial. The introduction of so-called dark factories, run entirely by robots with no need for artificial light or human presence further compounds the need for reliable systems. Unplanned downtime can be a manufacturer’s worst nightmare, potentially causing a backlog of products that can cost the company thousands. If a customer places an order with a next day delivery expectation, being just a day late is extremely damaging to the company.
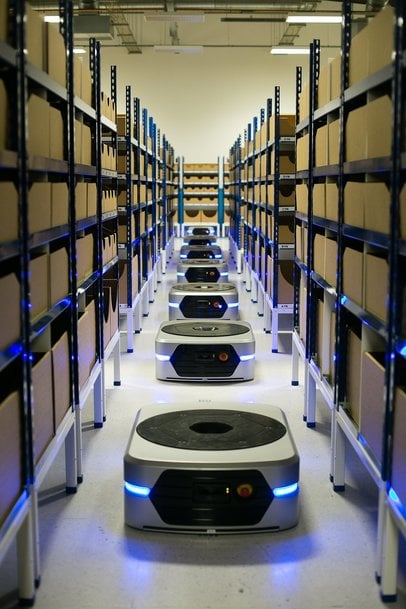
HepcoMotion’s proven V guide technology is consistently used for this very reason; reliability. Used across a broad range of industries and applications from harsh, dirty environments, to clean room environments and everything in between, HepcoMotion’s durable products provide a long system life. Celebrating its 50th anniversary this year, Hepco has a strong heritage built on a wealth of experience. Reliability has been proven time and time again with over half a century of applications. A further benefit is that spare parts are available for old systems - even those bought 50 years ago - providing much-needed longevity to investments.
Keep downtime down
Consumers now expect their online purchases to be delivered faster than ever before, which means those responsible for shipping and delivery need to operate around the clock. As such, many warehousing operations operate a 24/7 schedule. Minimising downtime is therefore key. Systems that can deliver continuous operation, without the need to be regularly stopped for routine maintenance such as re-lubrication, are highly valued by designers and production engineers the world over. Hepco’s V guide system has far longer re-lubrication intervals than ball rails for example, which means less frequent maintenance and less downtime required to keep them running. More so, even in the event of no lubrication, the V guide system will not fail catastrophically if it ends up running dry. Whilst this will reduce the system life, it is a useful feature that provides essential peace of mind in case a re-lubrication interval is delayed or overlooked for any reason.

With regards to bearing maintenance, speed is again key. When Hepco products show signs of wear, the process is simple and does not impinge too much on production time. The eccentric adjustment facility of the V bearings can be used to quickly and simply remove any play that has occurred. Moreover, when the V bearings reach the end of their calculated life, they can be replaced individually, and not as an entire set, saving both time and money.
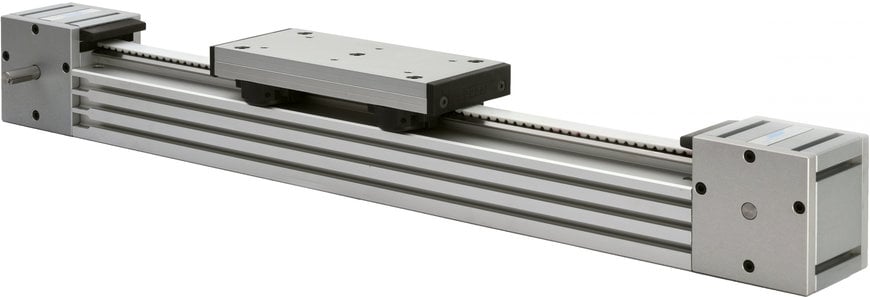
Coronavirus has caused behavioural shifts in consumer habits that has strong implications for the warehousing sector. The rise of online shopping has undoubtedly fuelled growth, placing new demands on the warehousing sector with a greater focus on efficiency and productivity. Automation is a crucial component in the future of this industry, providing an agile and effective response to logistical challenges. With over 42 major product lines with thousands of individual components, Hepco’s range of products can meet practically any warehousing requirement. Designed to offer high reliability to facilitate maximum productivity, HepcoMotion’s range of products are well-placed to serve this demanding, high duty industry.
www.hepcomotion.com