www.industry-asia-pacific.com
08
'20
Written on Modified on
Henkel expands gasketing portfolio with new technologies
New performance gasketing for the automotive industry.
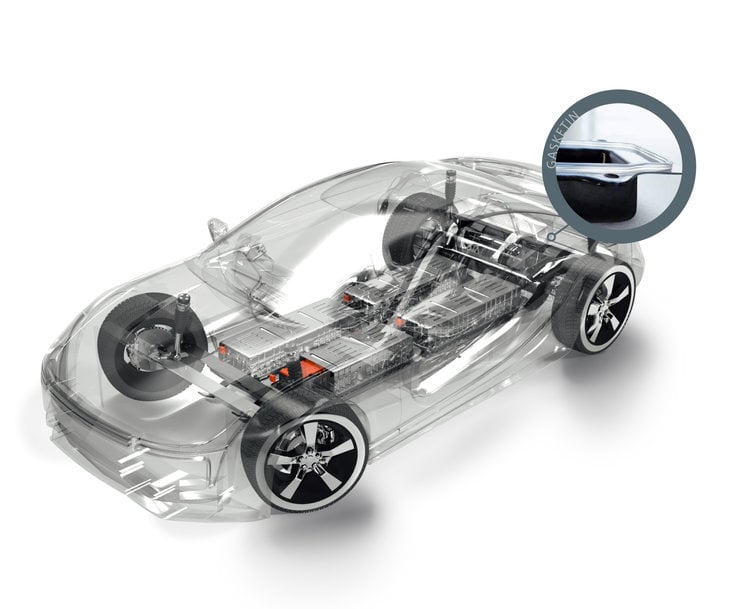
Henkel has recently expanded its gasketing product portfolio by including new materials and technologies that have been specifically designed for the automotive industry. With higher oil resistance and proven lower gas permeability, Loctite AA 5884 is a new polyacrylate gasketing technology that enables customers to enhance the performance and reliability of their products, all while achieving productivity goals and reducing overall costs.
The automotive industry is continually evolving, with stricter regulations and standards, emerging end-user requirements, and new product designs. The use of lightweight materials such as plastics has been a common strategy among automotive designers to help achieve their fuel efficiency and sustainability goals.
Engine covers, transmission covers and electronic components are being integrated into a growing number of plastic parts such as covers or header tanks, which need to be sealed to the core component unit. The most commonly used plastic-to-metal substrate sealing method is the press-in-place (PIP) process. This involves the solid rubber gasket or o-ring being manually applied onto the parts. This process brings with it a risk of displacement of the gasket during compression, however, which may lead to rework or leakages.
A milestone in the automotive industry
With the introduction of a new polyacrylate gasketing technology, Henkel has made the direct dispensation of a liquid gasket onto the customers’ part possible. These static gasket materials are positioned between two flanges which are held together by fasteners to prevent the leakage of fluids and/or gases, by closing the gaps between these surfaces. In order to keep the sealing function and a leak-free joint for a prolonged period, the gasket must be resistant to the medium being sealed. At the same time, it has to be capable of withstanding the application temperature, pressure and micro-movement of the joint. These gaskets are formed by applying a bead of liquid elastomer by using automated high-precision equipment.
The liquid gasket is cured by ultra-violet light within seconds and becomes a solid compression gasket with no knit line. This reduces the risk of re-work and leakages, while improving the productivity. It also lowers the overall cost by automating the gasketing process and eliminates the inventory and the complexity of the PIP solid gaskets.
The new polyacrylate gasket material has an excellent resistance against oil and ATF fluids and dose not promote oil foaming.
The new Loctite AA 5884 product marks a milestone in chemical and process development within the automotive industry. It delivers true benefits for the fast and efficient manufacturing of compression gaskets with a sustainability edge.
www.henkel.com