Anthony Machine and Kennametal Team-up to Reduce Setup Times
Texas job shop reaps the benefits of quick-change toolholders
For more than three decades, Kennametal’s KM™ brand of quick-change tooling has been making machine shops more efficient. As thousands of customers will attest, KM provides shorter setup times, greater flexibility, higher levels of machine utilization, and the ability to meet the industry’s increasingly stringent requirements head on.
One of these is Anthony Machine Inc. Since 1946, the San Antonio job shop has served a variety of industries, including oil and gas, mining, transportation and power generation. With all that precision machining experience, there’s little this San Antonio job shop can’t handle. However, after the company purchased a pair of NLX 3000 1250 universal turning centers from CNC machine builder DMG Mori—the shop’s first Y-axis, live-tool lathes—Anthony’s manufacturing team was challenged with making the most of that new investment.
Kennametal senior sales engineer Mark Davis was there to help, just as he’s been for the past decade. He explained to Anthony that the best way to reduce setup times and maximize the new machines’ potential would be to equip them with Turret Adapted Clamping Units (TACU) and KM quick-change toolholders.
“The TACU system supports everything from KM32 up to KM63,” Davis says. “We offer blocks for both static and driven tools, and can tool up lathes from Okuma, Haas, Mazak, Doosan, and of course DMG Mori—pretty much all of the major machine tool builders, with more coming online all the time. This makes it both easy and cost-effective for our customers to equip more than 80 models of CNC turning centers with a fast, flexible and accurate quick-change toolholding system.”According to Anthony Machine manufacturing technologist Daniel Goller, the decision to adopt TACU and KM for the new machines was an easy one. “Over the years, we’ve built a number of KM-equipped custom toolholders for deep boring and other machining operations on our CNC lathes and machining centers, and we use Kennametal? on several of the shop’s manual turret lathes to overcome limitations with available tool positions,” he says. “On more than one occasion, we’ve earned new business because KM was able to achieve tolerances and surface finishes that others couldn’t do with conventional tooling.”
Anthony’s operations manager Mohsen Saleh agrees. “The differences are striking,” he says. “Compared to the traditional wedge and screw-style blocks that come standard on most machines, the KM-equipped TACU units are both faster and more accurate. We routinely hold tolerances of 0.0005" (0.013 mm) and I’m told that part size doesn’t change from one clamping to the next. The turret’s less crowded, everything’s easier to get at, and you don’t have the chatter and deflection that you often find with your typical straight shank tools and set-screw type boring bar holders.”
“Anthony’s experience with TACU is what we’ve come to expect from KM,” notes Kennametal’s Davis. “Considering the breadth of the platform, its accuracy, and especially its flexibility, it’s quickly become the de facto industry standard in quick-change tooling.”
Saleh summarizes Anthony’s recent success with a bit of company perspective. “We bought our first CNC machine in 1986,” he says. “At that time, we were using a well-known competitive brand, and then Kennametal came knocking. What first struck us was their service-oriented attitude. They’ve always been willing to come in and work with us on applications, which together with the quality of their products is why they’ve since become our preferred tooling supplier. We’re always competing against smaller, lower-cost shops, and in order to continue winning new business in this environment, we have to adopt the latest in advanced tooling and machine tool technology. This is what’s given us the edge, and Kennametal is a big part of it.”
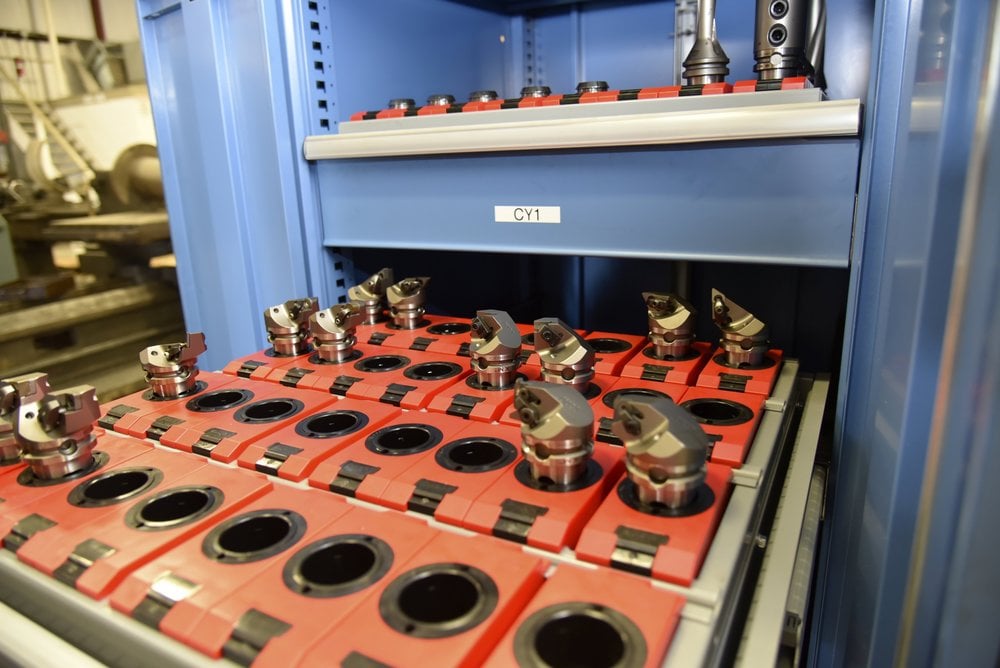
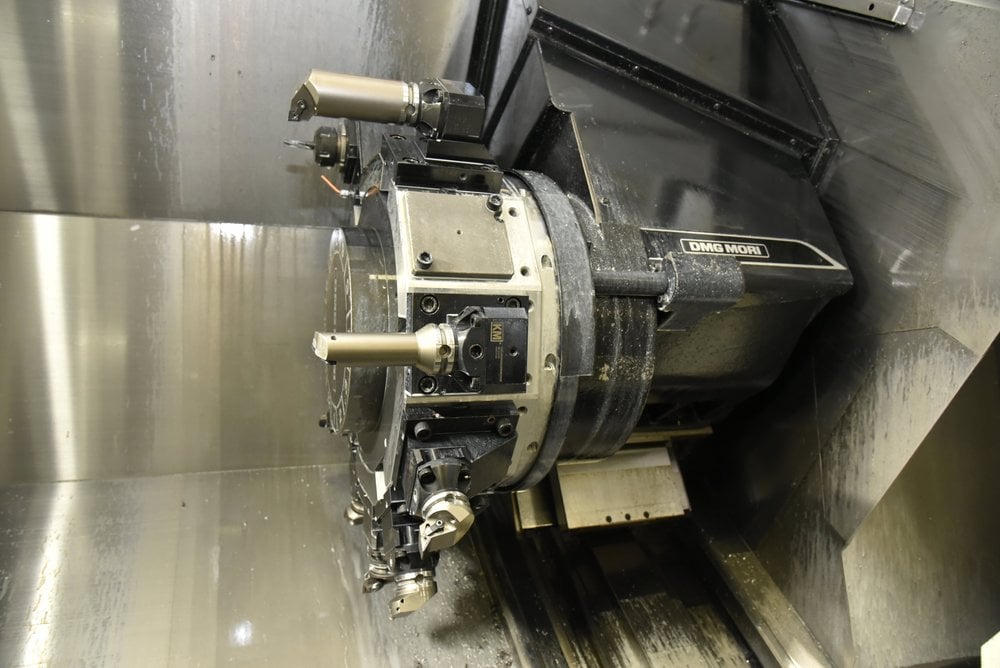
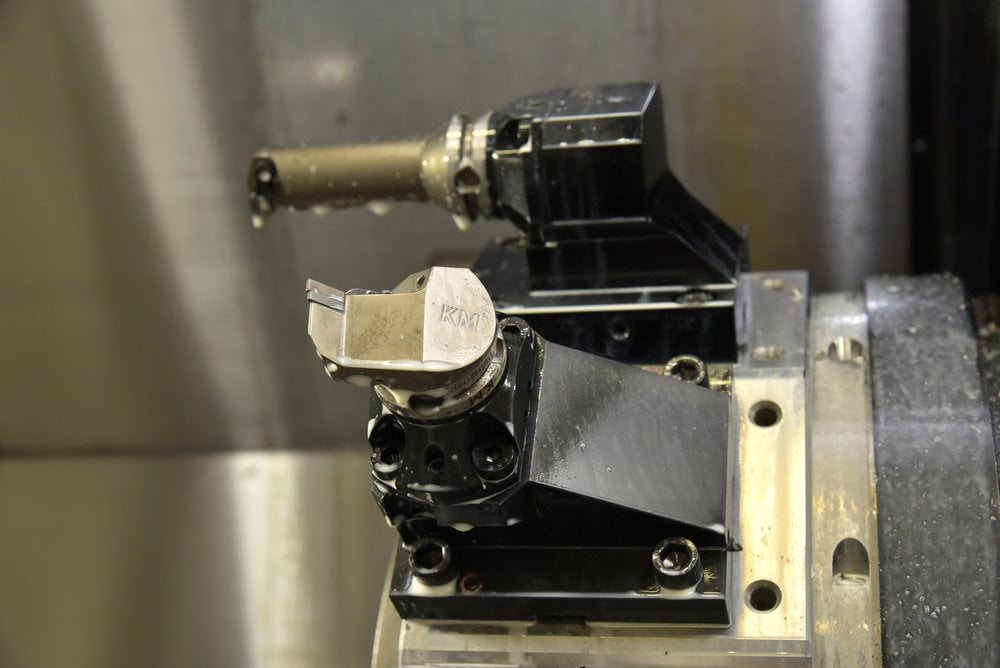
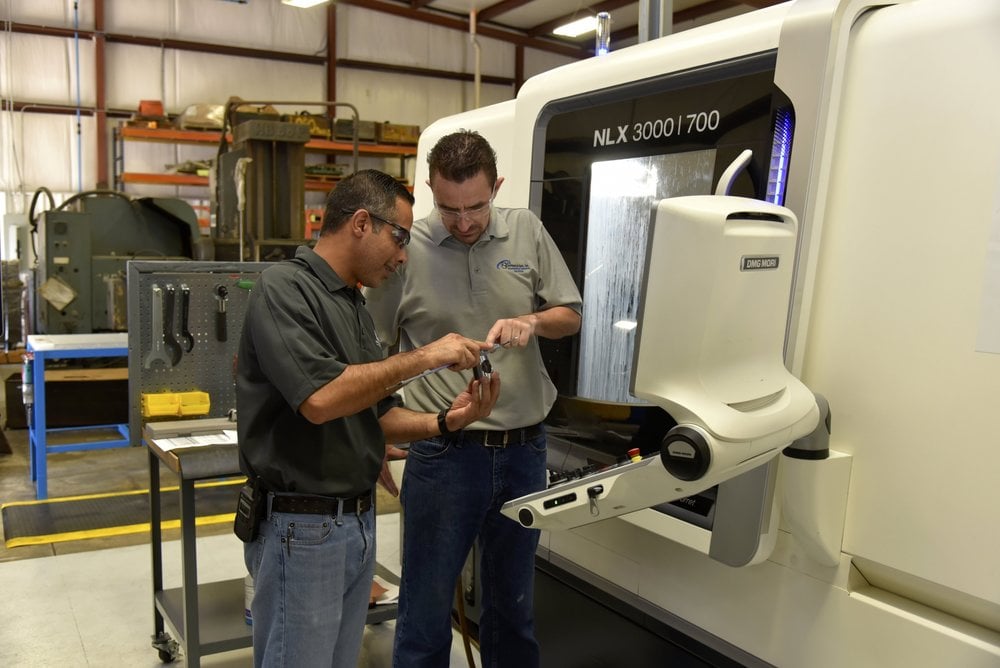