www.industry-asia-pacific.com
12
'18
Written on Modified on
Morgan Advanced Materials reduces energy waste in foundries with Blue Lightning Thermocouple Assembly solution
Foundry owners could be wasting money and operating inefficiently by failing to use an accurate and continuous method of measuring the temperature of molten metals in holding furnaces prior to casting.
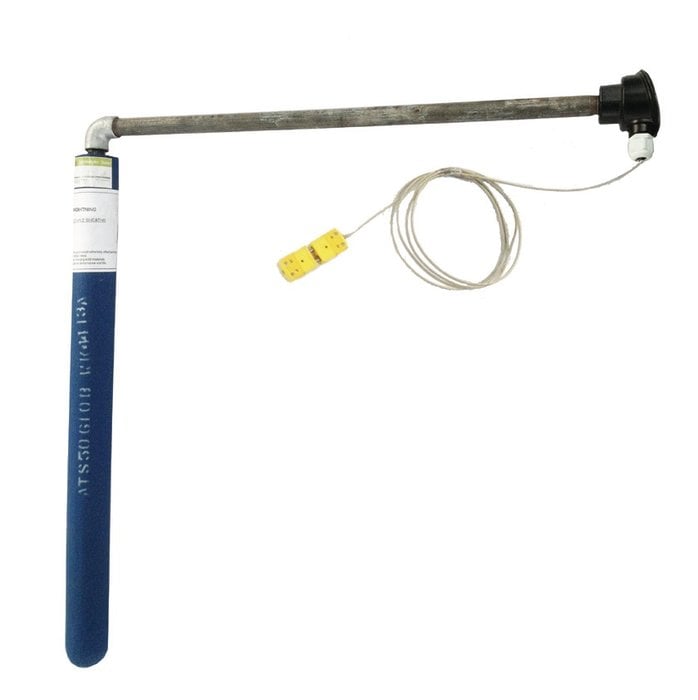
Consistent high temperatures are required in holding furnaces, where metals – notably aluminium – must be kept in a molten state prior to casting. Some foundries measure only the outer furnace temperature, while others do not measure the temperature at all. Either approach is inefficient as operators tend to overestimate the temperature required, and therefore spend more on energy.
For a more accurate measurement, thermocouple sheaths are dipped into the molten metal. The material traditionally used for this purpose, cast iron, has its drawbacks compared to the clay graphite used in the manufacture of Blue Lightning.
Mirco Pavoni, Global Technology Director of Molten Metal Systems at Morgan Advanced Materials, explained: “Cast iron will quickly degrade, meaning sheaths have to be replaced regularly. There is also the risk of cross-contamination of iron particles mixing with molten aluminium. To prevent this, iron thermocouple sheaths are coated with a protective material; a daily process that wastes valuable foundry labour time.”
The answer from Morgan is the Blue Lightning Thermocouple Sheath manufactured in a special clay graphite construction. This material is neutral and inert, eliminating the risk of contamination and protecting the purity of the molten metal. Clay graphite also offers exceptional thermal shock resistance, meaning that Blue Lightning lasts considerably longer than cast-iron sheaths and can withstand temperatures up to 2,192 degrees Fahrenheit (or 1,200 degrees Celsius).
“Using Blue Lightning, an accurate reading can be achieved in just three to five minutes, faster than cast iron because of clay graphite’s superior conductive properties. This enables foundry operatives to adjust the temperature quickly, further reducing energy wastage,” says Mirco.
Morgan’s Molten Metals business supplies Blue Lightning as a full thermocouple assembly to support foundries looking for a single supplier. In tandem with Morgan’s expertise in advanced composite materials, this makes Blue Lightning a truly comprehensive system for the measurement of molten metal temperature
Two types of pyrometer are available to suit the specific set-up of a foundry. “Blue Lightning is equally accurate whether used with a fixed pyrometer, which measures the temperature towards the bottom of the crucible, or a floating pyrometer for applications where foundries take their molten metal from near the top,” confirmed Mirco.
For further information please visit: http://www.morganmms.com
For further information, please contact:
Simon Kinnear, Wyatt International
This email address is being protected from spambots. You need JavaScript enabled to view it.
Tel +44 121 454 8181
Francesca Minett, Morgan Advanced Materials
This email address is being protected from spambots. You need JavaScript enabled to view it.
Tel +44 (0)1299 827000