www.industry-asia-pacific.com
29
'21
Written on Modified on
STRABAG AND PERI CONSTRUCTING AUSTRIA’S FIRST BUILDING USING 3D PRINTING TECHNOLOGY
Austria’s first 3D-printed building is being constructed in Hausleiten, Lower Austria. Construction technology group STRABAG, together with PERI, the formwork and scaffolding manufacturer and a pioneer in 3D concrete printing, is realising a roughly 125 m² office building next to its asphalt mixing plant in Hausleiten. The special dry mortar for the construction 3D printing project, with long workability and good pumpability, is being supplied by Lafarge.
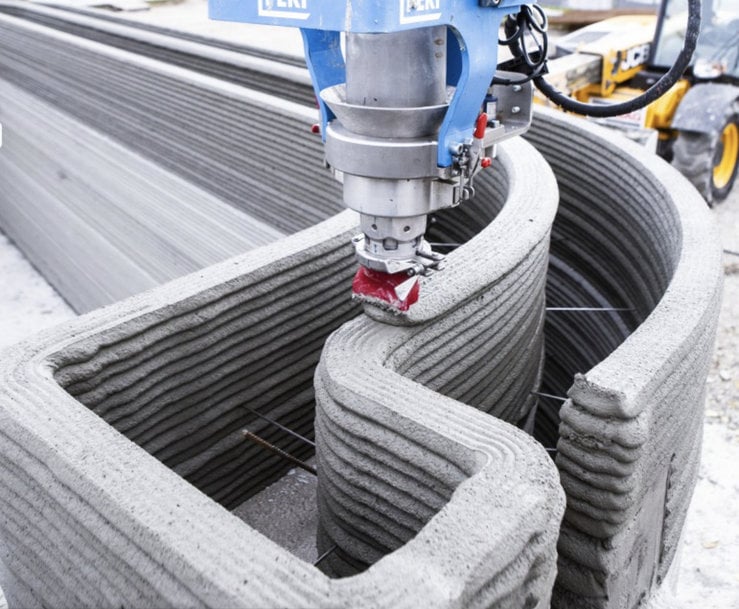
“3D concrete printing gives the construction industry an important boost of innovation and represents an exciting addition to the range of available construction methods. With this practical test, we want to further develop the technology of 3D concrete printing together with our partners PERI and Lafarge. The joint planning and design for Hausleiten has already yielded some important insights for the future,” says Klemens Haselsteiner, the STRABAG Member of the Management Board responsible for digitalisation and innovation.
“At PERI, we believe in the enormous potential of the fledgling technology of 3D concrete printing. Just under a year ago, we printed Germany’s first residential building using a BOD2 printer from our Danish partner COBOD. Since then, the PERI team has successfully realised several additional printing projects. Together with our partners STRABAG and Lafarge, we are now bringing this new form of construction to Austria and are pleased to be realising the first 3D-printed office building in Hausleiten,” explains Thomas Imbacher, Director of Innovation & Marketing at PERI AG.
Enormous potential: complex designs in a short amount of time
Construction 3D printing offers several advantages where its use makes technical and financial sense. The COBOD BOD2 gantry printer used in Hausleiten can print concrete at up to one metre per second, which significantly shortens the construction time. The structural works for the building in Hausleiten can be completed in around 45 hours of pure printing time. Construction 3D printing also offers significantly more design freedom compared to classic concrete construction, with the possibility of easily creating architecturally complex rounded designs.
“3D-printed buildings will help to establish a new, digitally and environmentally advanced language for concrete. The intelligent material is convincing in its application and provides a high degree of architectural freedom in design. It allows us to build more with less,” says Berthold Kren, CEO of Lafarge Austria.
Technology and training to combat the skilled labour shortage
“Currently, 3D printing is only suitable for construction projects up to a certain size, so having a skilled workforce remains crucial for the successful realisation of construction projects,” Thomas Birtel, CEO of STRABAG SE, points out. “The severe shortage of skilled labour that currently prevails will remain with us in the future as a challenge that we have to cushion with two strategies: by investing in training, for example with our new STRABAG Camp[us] Ybbs, and by increasing productivity with new technologies.”
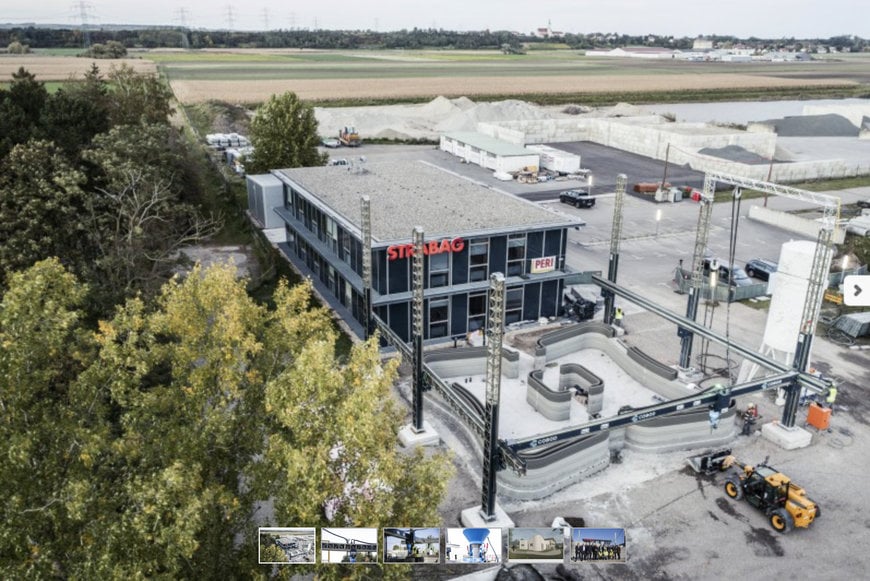
Background knowledge: How does 3D concrete printing work?
PERI is using the COBOD BOD2 gantry printer for the construction printing project in Hausleiten. This printing technology comes from Danish manufacturer COBOD, in which PERI acquired a significant stake in 2018.
The print head moves about three axes on a securely installed metal frame. This allows the printer to be moved to any position in the structure being built, requiring only a single calibration. The 3D printer applies the print material (dry mortar) in layers to create the walls. Laying down two parallel printing paths creates a hollow wall that is then backfilled with cast-in-place concrete as a load-bearing system. To create the outer wall, a second cavity is formed by printing another mortar path further outside the previous wall and filling this with thermal insulation material. The printed walls can be regarded as a kind of lost formwork system.
During the printing process, the printer already takes into account the water, electricity and other utility lines and connections that will be installed at a later point. The BOD2 is certified in such a way that work can also be carried out in the print room during the printing process. This allows manual work, such as the laying of pipes and connections, to be easily integrated into the printing process.
The printing material is stored in silos. The ready-to-use dry mortar is then pumped directly into the print head during the printing process after the addition of water. The Tector Print brand material used for printing the office building in Hausleiten was developed by Holcim and is adapted to the special requirements of 3D concrete printing.
www.strabag.com